Many food and beverage companies seeking to increase capacity in response to consumer-driven success are finding it difficult to quickly bring new facilities online due to current market conditions and continued supply chain disruptions. The longest lead times on major materials that most in the industry have ever seen are making the construction of new buildings and building expansions especially challenging. These factors, exacerbated by shifts in consumer preferences sparked by the pandemic, are causing a number of growing food and beverage companies to retrofit existing space or build out a speculative warehouse development in lieu of traditional build to suits.
Lasting Pandemic Effects
The staggering growth of cold storage facility development and construction has been sparked by a number of factors. The pandemic accelerated shifts in consumer preferences and created lasting effects on demand and delivery expectations throughout the cold storage industry, especially for companies in the grocery and direct-to-consumer spaces. In addition, supply outpacing demand has led to the majority of remaining opportunities being in existing facilities that are out of date and require significant upgrades to run efficiently and meet code requirements.
While the rapid growth experienced during the onset of the pandemic wasn’t sustained, increased consumer awareness and adoption has continued to drive success for food and beverage companies, leading to an increase in demand for cold storage, food processing and production space. These companies have had an influx of revenue and now there are more building owners that are actively pursuing cold storage and food processing leases.
Additionally, same and next-day delivery expectations set during the pandemic are here to stay, making speed to market and facility location vitally important for companies seeking to increase capacity.
Benefits Of Retrofitting
Choosing to retrofit an existing space rather than build new allows companies to operate sooner by six months or more. With timeline and proximity to population centers driving many decisions, owners who choose to retrofit have the potential to simultaneously prioritize schedule and location. As the booming industrial market continues, new building developments are occurring further away from population centers. Additionally, owners who choose to utilize design-build as their project delivery method can further improve their schedule and hedge against longer lead times in a project’s earliest stages.
Speed-To-Market Benefits
In today’s challenging market, the industry continues to see long lead times for key materials such as joist/girders/deck, which have seen increases from four months to 12 months for procurement over the past year. As owners look to keep up with demand, retrofitting an existing facility can allow for increased production capacity to occur months earlier than it would when building a new facility. In a speculative environment, owners obtain the benefit of first-to-market advantage when leasing an existing space.
Prime Location Benefits
In addition to increased demand, there has been a push to move perishable products through the cold chain at speeds quicker than ever before. Because of this, locations that offer not only easy access to transportation infrastructure capable of reaching a large customer base, but also proximity to raw materials, packaging, and labor are highly sought after.
While existing cold storage assets are primarily located within the core of highly populated regions, new developments are moving further and further away from urban areas due to continually increasing land costs. Choosing to retrofit allows owners to capitalize on the strategic location benefits of their current facilities, while avoiding the challenge of rising costs.
Space Utilization Challenges
In circumstances with a highly complex equipment matrix, retrofitting may not be the best option due to highly coordinated processing designs not fitting within the footprint of the existing facility. Additionally, accompanying floor slope requirements may involve removing portions of the floor slab.
However, in ideal settings, retrofitting facilities can allow for the space needed for automation, equipment, and process line upgrades when increasing overall capacity. Whether retrofitting an existing facility or building out a new speculative warehouse development, through strategic design decisions, owners can sometimes achieve desired upgrades in the already established footprint.
Analyzing key elements that drive design such as packaging methods, outbound shipping, and dry packaged flow, equipment footprint and impact on utilities, equipment relocation or modernization, and flow of ingredients or raw materials into the building through storage and into production, allows for the most functional use of the space. Expert sequencing of these specifications also aides in effective master schedule development.
Additionally, those who choose to retrofit an operational facility gain the benefit of being able to integrate upgrades into their current operations and utilize their already trained workforce.
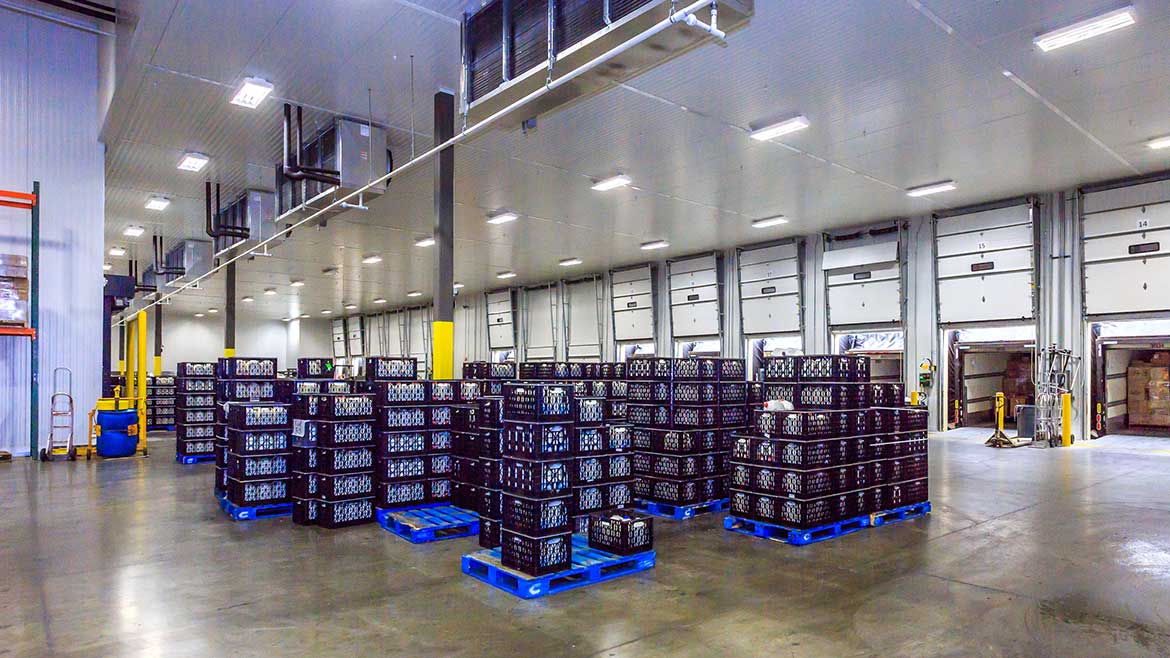
The Design-Build Difference
Owners can expand upon the benefits offered from retrofitting through design-build project delivery, including quicker delivery and tackling current market challenges. Unlike traditional delivery methods that treat the phases of design and construction sequentially, the design-build process combines quality of design and construction, management of capital expense and schedule all under a single point of responsibility.
Preliminary design is completed during the proposal process, and owners benefit now more than ever from the speed at which design-build delivery moves. Once a project is awarded, the design-builder can move swiftly through design and buyout to lock in material pricing. Under normal circumstances, this offers a substantial advantage over the traditional design-bid-build delivery process, but in current conditions, the benefit is not only advantageous; it’s critical to overcoming market challenges and supply chain disruptions.