The food industry is undoubtedly one of the most important sectors in our economy. While this may be common knowledge for many—the industry is recognized as a necessity, after all—what isn’t as widely known are the basics of the manufacturing process, and the software and technologies used to ensure everything runs smoothly. For example, when a machine breaks down in a food processing plant, it can cost the manufacturer several hundred thousand dollars an hour.
Fortunately, Industry 4.0 and IoT have ushered in new ways to protect the process of making food for the masses. Food manufacturers use software that tracks the status of the machines and predict when repairs will be needed, while others check the quality of the food to make sure it’s safe for consumption. These are vital components within a food manufacturing plant, and IoT-focused solutions can help food manufacturers increase energy efficiency.
However, IoT innovations often aren’t used because of concerns over cost, how long it will take to train people to use the technology, and the overall value of running a truly connected manufacturing facility—the “if it isn’t broken, why fix it” mentality. This article will go over the several roles that IoT systems play in the industry, why it’s important, how these systems are underutilized, and how companies in the industry benefit from them.
Roles Monitoring Systems Play
There are several roles that monitoring systems play in helping food processing facilities become more energy efficient. One element, in particular, is energy consumption. This is a machine parameter, and as such, it can—and should—be monitored and analyzed at all times of machine and production line operation. It’s imperative to monitor energy consumption at the lowest component level possible. By doing so and analyzing energy use over time, food processing facilities will be able to obtain visibility into the potential areas of design that are causing high consumption levels.
For example, suppose you can monitor how much energy each asset consumes while changing your output when manufacturing certain food products. In that case, you can find ways to show how much waste there is and begin finding solutions. Ultimately, you’re wasting energy at a high rate if one part is not running efficiently. If that’s happening, it will disrupt the entire process. That’s why having a full dashboard view of all your assets is so critical to maintaining energy efficiency.
The Importance Of These Systems
With technology quickly advancing, intelligent monitoring and data collection are essential. All food manufacturers should consider how they can leverage machine data to decide how to manage those assets. Some CMMS software offers a next-level solution for maintenance that will include remediation triggers that alert personnel that an asset has reached an alarming level and communicate what actions and instructions are needed and by whom in the company. Additionally, monitoring systems that keep track of food quality and manufacturing accuracy are vital because they provide extensive traceability and inventory management features. And, on the energy efficiency side, closely monitoring the machine’s performance is paramount to hitting target goals.
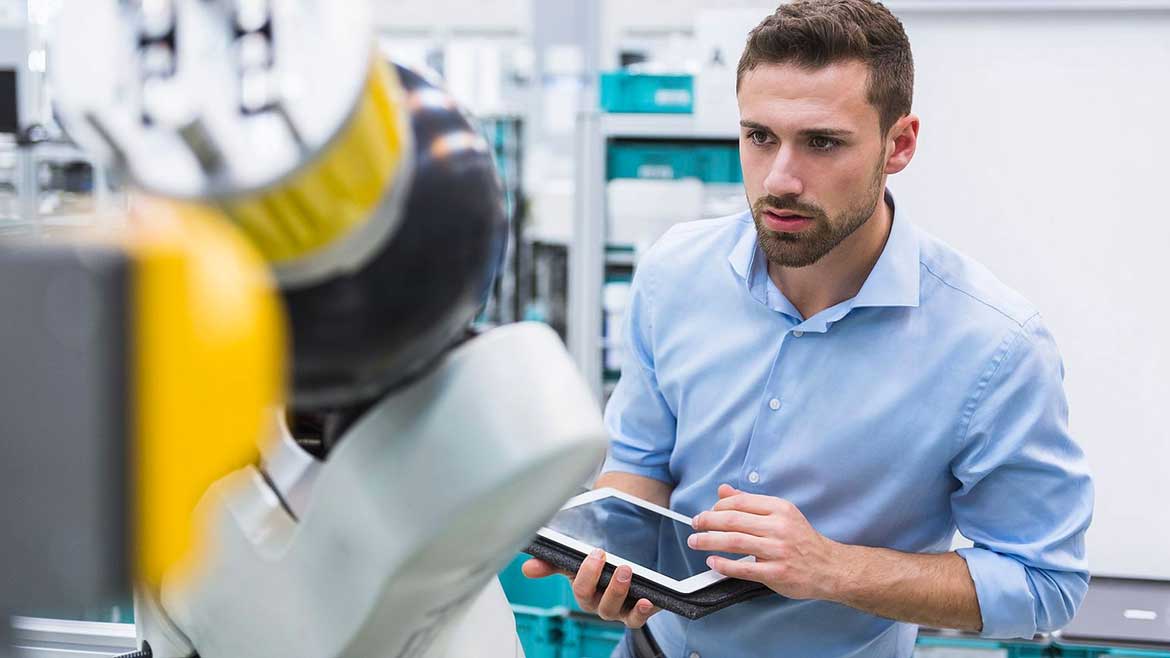
Why Is Software Overlooked Regarding Energy Efficiency?
The software can help manage assets and do things such as notify a manager when there are higher than usual levels of energy usage or trigger orders for proactive repairs to reduce energy consumption. However, energy levels aren’t always utilized, and food manufacturers don’t always consider this solution when measuring energy efficiency.
Part of the problem is that not enough companies are using real-time data across all the assets in their facility. Without a full dashboard view of everything, it’s difficult to pass along accurate information to decision-makers and make predictive decisions that will reduce things like energy consumption.
Moreover, because of legacy equipment, some companies may still be focused on line level monitoring rather than component level. While Industry 4.0 does not mandate wholesale replacement of systems, it has made the process of retrofitting sensors onto equipment and adding monitoring capabilities much more affordable and nimble.
AI will also begin taking its place. Examples, of course, include adding to the predictive accuracy of notifications and analysis. However, other application areas will consist of using AI to understand subtleties leading up to an event that will add intelligence to understanding the root cause and add a higher level of specificity in improving future remediation actions. AI revealed outcomes would also improve core engineering and design enhancements.
For example, you could see the difference in energy efficiency, as it could be worse by 3 p.m. versus 2 p.m. With this information, you could determine why the situation is occurring and find the weakest link. This allows you to be more proactive about remediation: not just knowing that a machine is less energy efficient, but automatically doing something about it to curb the issue.
From food processing plants to cold storage and distribution facilities, focusing on energy efficiency and safety at the software level provides a unique view under the hood of all your assets. In my experience, companies exploring advanced IoT monitoring systems tend to streamline their processes more efficiently. Not to mention, employees can get work done faster.
Companies on the leading edge of the industry are taking advantage of advanced Industry 4.0 software to predict outcomes and better automate their facilities. The obsolete ways of monitoring are no longer going to make the cut in today’s age. Companies that invest in software to monitor assets across the facility have shown tremendous ROI tracking—everything from efficiency to reduced downtime with machines. In an era where every minute counts, the investment can be worth it.