Almost nothing in the cold supply chain moves without the help of lift trucks. They’re so ubiquitous it’s easy to forget how vital they are in the transportation of goods to and from cold storage areas. The demand for cold retail foods in the wake of COVID-19 has made it even more important for forklifts to operate with speed and precision to maintain continuous levels of productivity.
Since 2020 marks the 30th anniversary of Refrigerated & Frozen Foods, we take a look at the evolution of lift truck technology and what current trends are shaping the future of forklifts for cold food operations.
Lift Lore
“In the late 1990s and early 2000s, we saw the rapid expansion of AC powered lift trucks,” says Michael Field, president and CEO, The Raymond Corporation. “Within the last 10 years, we have seen the emergence of lithium ion batteries, telematics and automation.”
Those technological advancements for forklifts have, in just a few decades, created greater energy savings than ever before, reduced down time for repairs, and added higher levels of efficiency due to constant monitoring of lift trucks by telemetry.

Today's lithium-ion battery technology can communicate with lift trucks like these from Hyster and adjust performance based on operating temperatures.
“The 2000s saw a tipping point in consumer electronics that created something of a ‘Big Data Bang.’ High-speed internet connections reached mobile devices and thus began a new digital era that connected virtually everyone and everything. The connected world has grown at an astounding pace ever since; from 2 billion smart devices in 2006 to an expected 200 billion by 2020. This has led to an explosion of information and terms like the Industrial Internet of Things (IoT), big data, 5G and the cloud becoming common vernacular,” explains Kevin Paramore, emerging technology commercialization manager, Yale Materials Handling Corporation.

Premium Power
Like Field mentioned earlier, battery technology has evolved rapidly the past 30 years, and while traditional combustion engines and lead acid batteries are still options for forklifts, today’s environmentally friendly, energy-efficient lift trucks can utilize hydrogen fuel cells—where refueling takes just minutes with zero emissions during operation—or rechargeable lithium-ion batteries.
“Lithium-ion batteries are a strong choice for cold temperature food handling operations,” notes Paramore. “As an electric source, they avoid the emissions of internal combustion engines, but unlike other electrification options, they can operate in a broad temperature range, from -40 to 113-degrees Fahrenheit.”
Lithium-ion batteries are also smaller than their lead acid predecessors and combustion engines on a forklift. As a result, driver comfort can be built into today’s lift trucks in ways that weren’t possible before due to space constraints inside the cabin. This has also helped create lift trucks designed for cold conditions that didn’t exist 30 years ago.
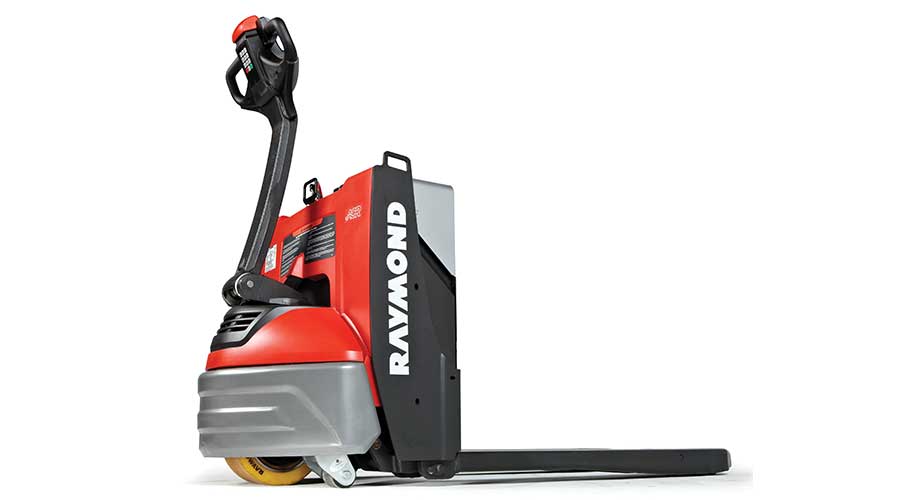
“One effect of operating in such challenging environments is a frequent buying cycle—cold and frozen food operations replace 5% to 8% of their lift truck fleet annually. Lift truck manufacturers now offer cooler/freezer and subzero packages designed to help protect components, along with features designed for operators, like heated cabins, handles, and floors, helping boost comfort, productivity and staff retention,” says Steven LaFevers, VP of emerging technology at Hyster.
When a lift truck battery needs replenishing at its charging station, Paramore says operators can save money by paying close attention to utility details. “Many markets have a dependable electric grid, but some rural areas can suffer from insufficient capacity that could require costly upgrades, while urban centers can fall victim to brownouts,” he says. “Another factor is the risk of increased utility rates during peak hours. Operators can avoid this by staggering charging schedules to avoid overtaxing electrical grids during peak times. Both combustion engines and hydrogen fuel cells offer opportunities to store fuel on-site, minimizing dependency on public utilities.”
Field adds that Raymond just completed phase one of a project that would use solar panels to send energy to a micro grid within a storage facility, generating in-house power for forklift charging.
Transformational Telemetry
Another tech advancement that has changed forklifts is telemetry, which, through a combination of data-collecting sensors and cloud-based software, monitors every aspect of a lift truck in real time to expose inefficiencies of usage and anticipate repairs, preserving productivity and ultimately saving money.
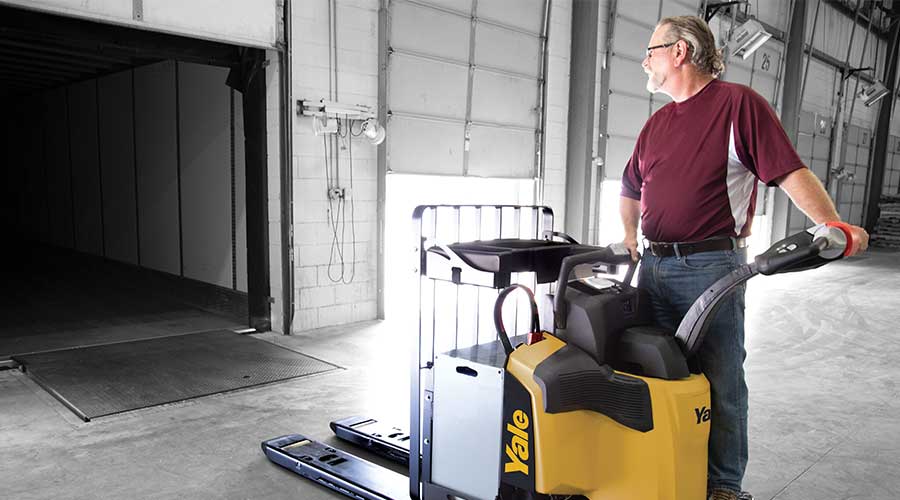
Lift truck telemetry monitors all aspects of a vehicle's use in real time, helping fleet managers anticipate maintenance and know when a forklift has sustained collision damage.
“Lift truck telemetry enables businesses to assess which employees may be triggering avoidable damage and could use extra safety training. For example, advanced collision detection and real-time impact alerts help improve fleet safety awareness and reduce avoidable damage. Telemetry can protect equipment from prematurely returning to operation following a critical impact. Operations can also restrict access to lift trucks by ensuring only operators with proper licensing and training are able to start equipment,” LaFevers says.
Monitoring maintenance needs through telemetry is “especially important for trucks working in tough environments like refrigerated and frozen food facilities,” says Paramore. “The ability to evaluate maintenance information alongside expected demand and specific truck applications lets fleet managers make quick and informed decisions about fleet size and composition. This helps them continuously improve operations and maintain a right-sized fleet composed of equipment tailored to meet their specific operational challenges and eliminate the cost of running excess trucks.”
Autonomous Advances
Perhaps the most discussed and frequently trending option for lift trucks has been automated guided vehicle (AGV) technology. Over the past 30 years, autonomous technologies have “blossomed into well-developed, ready-to-deploy solutions. Early materials handling AGVs required extra infrastructure like ground wires, tape, magnets and reflectors to navigate fixed routes. Today’s robotic lift trucks do not require any infrastructure and can adjust routes on the fly. This offers great strides forward in terms of flexibility, ease of use and productivity,” says Paramore.
AGV technology can be found in every type of lift truck today to meet the needs of cold storage facilities, including end riders, tow tractors, counterbalanced stackers and robotic reach trucks.
Staff Safety
While AGV is a rapidly evolving option for lift trucks, the industry hasn’t yet reached the point where every cold storage facility features driverless forklifts. However, technology surrounding the still-necessary drivers in their cold storage environments has made it safer than ever to move inventory, including loading dock levelers to prevent “dock shock” where lift truck drivers are jolted by uneven surfaces, causing injury. Brighter LED lights have made it easier for operators to navigate their loads into and out of trucks, motion sensors around the loading dock alert drivers of approaching hazards, and drive-through docks keep warehouse temperatures steady.
“Cold foods facilities produce different challenges than standard environments. Because it’s important to maintain colder temperatures, even the slightest amount of moisture can become increasingly slippery,” says Chad Dillavou, director, product management, Rite-Hite. “Drive-through docks, which keep refrigerated air inside the facility, keep energy costs down and minimize precipitation from entering a loading dock area, which in turn reduces slick surfaces that can lead to injury or product damage.”