Almost every cold foods facility reaches a crossroads where a decision must be made to either move into a larger, new-build structure capable of handling a company’s business growth, or take the renovations route to update and expand an existing building.
“Renovations can update and fix a lot of problems, but more importantly, it gives you the opportunity to redesign the facility to match the requirements of your customers,” says Steve Tippmann, executive vice president, Tippmann Group. “In the public refrigerated warehouse business, I would look at location first, labor-efficient design second, and energy cost third and decide if the project should be a renovation or new-build. In food processing facilities, food safety, labor and design efficiency, and capacity are the major drivers in the decision.”
Aside from cost considerations—a new-build, greenfield project is often more expensive—deciding to renovate a cold facility hinges on several complex business assessments. We asked Tippmann and other design-build experts for their advice regarding building upgrades, and what questions an owner should ask before committing to a project.
Assessing the Need
“There can be several indicators that a facility needs an upgrade,” says JD Boone, senior project manager, A M King. “At its most basic, the trigger for this decision is a desire to amplify supply to meet an increased demand. But there can be other incentives, such as outdated equipment and systems, quality and safety of employee work environment and master planning to help with speed-to-market for new product lines. These less obvious triggers can be more difficult to analyze and sometimes challenging to sell as a benefit to upper management.”
Energy savings realized through renovations can provide a quantitative measure to convince owners to invest in an upgrade, so energy and safety audits can help pinpoint exactly where work is needed. “Wear and damage in a facility speaks for itself, but energy consumption and labor efficiency are big drivers in the success of a business, and many times a major renovation can improve efficiency and help with those costs,” Tippmann says.
The finished renovation of Southern Foods' meat, seafood and cheese processing plant in Greensboro, North Carolina. Photo courtesy of A M King.
Location and Logistics
The real estate a facility sits on can be just as vital to a company’s operations as the equipment and production within its walls. Location determines the speed of distribution for products, and employees populating a facility are usually drawn from the surrounding area. To move to a new building in a different location might mean starting over in both areas, so many companies opt to renovate rather than relocate.
“We had a job in Colorado where the owners said even though it was going to cost them twice as much to renovate as opposed to moving and building on a greenfield site, they opted to renovate because the investment to purchase new ground and start from zero was punitive for their operation and speed-to-market standpoint,” says Forrest McNabb, president of Big-D Construction. “You may also have a long-term relationship with the fire department or city building officials and inspectors in your area, and when you pick up and move, you have to build those relationships all over again.”
From a productivity standpoint, employees at an existing facility likely know every inch of the building and how to operate it for maximum daily results. “There is great value in tribal knowledge that exists with the employees and people that manage a facility. Learning to operate a new facility can come with a steep learning curve if not executed properly,” says Boone.
Vertical construction to expand square footage in cold storage facilities by making the ceilings higher is among the most requested renovations today. Photo courtesy of Tippmann Group.

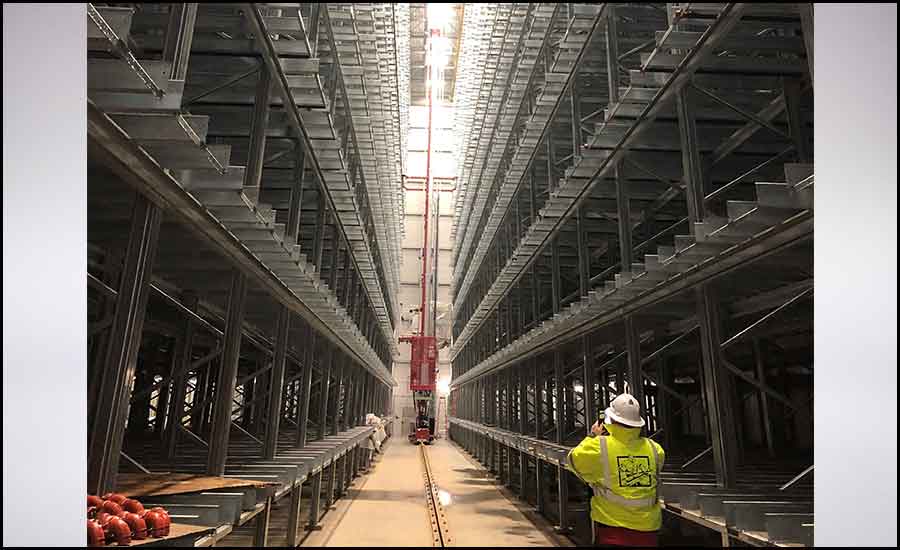
An expanded, renovated facility can be preferable to building a new structure on a greenfield site if a company wants to maintain their geographic location for distribution logistics, and their employees drawn from the surrounding area. Photos courtesy of Big-D Construction.
Price and Productivity
While the example McNabb noted earlier was a rare renovation costing more than a new-build project, the price of a new-build facility, on average is between 40% and 60% more than a rehab, and can take twice as long as a renovation project depending on what is being upgraded, according to Boone.
“There are also other advantages that are not considered right away. New infrastructure and utilities can be a large expense for food facilities—between 20% and 30% for new-builds. In most cases the infrastructure that is already in place at an existing plant can be added onto and re-worked to accommodate the changes,” Boone says.
While cost and time are advantages to a facility rehab, a company should be prepared for construction disrupting the daily flow of business both inside and outside the building. “If you’re upgrading an operational facility, that work can take anywhere from nine to 24 months, because of the precise, surgical work needed to keep the business operational without impacting productivity,” notes McNabb.
Carl Morse, senior project manager at A M King, adds, “Site logistics for a renovation can become a pinch point too. Greenfield projects have much more flexibility, but expansion projects must contend with operational and construction traffic. Sometimes there is not enough space for both. In the past, space has been rented from adjacent properties to accommodate a laydown area for material to be used onsite.”

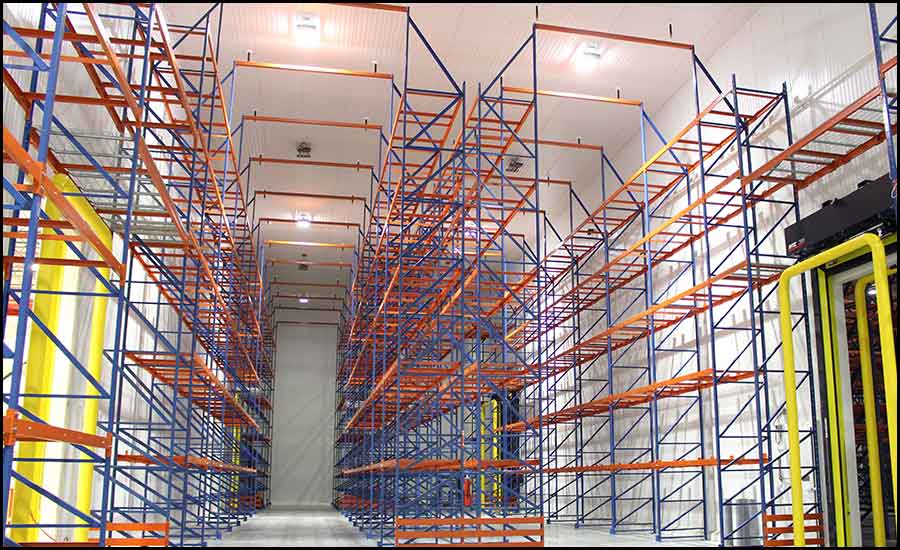
The increased demand for cold foods has made it necessary for cold storage facilities to expand their square footage and number of pallet positions to keep up with market needs. Photos courtesy of Tippmann Group.
Requested Renovations
Our experts mention the most popular upgrades to cold facilities today are automation for food processing and logistics within a building, and energy-efficient materials and equipment. For cold storage properties in particular, extending the height of a building to accommodate more pallet positions rather than expand the existing real estate footprint outward is a common cost-saving choice for facilities with limited property.
“The big three right now are anything to do with energy efficiency, greater automation, and vertical construction,” McNabb explains. “Vertical construction can be tricky depending on location and season. Snow drifts become an impediment with roof work, especially with functioning operations. So in those climates, you can't necessarily go above the existing roofline without retrofitting the existing roofline or making significant alterations to the roof. But if that’s the only place they can grow, then you just need to accommodate it and think through that process thoroughly.”
Boone says his company is being asked to develop and complete renovations faster than ever to decrease downtime and lost productivity, especially with demand for cold foods at record levels today. “Owners have been relying on us to be as flexible as possible. With extended lead times, some trades and scopes have been released earlier than before in the overall design-build process. The typical design process continues even though material is on the way. As those owner requests and design changes happen, clients are looking to us to make it work and stay within budget.”
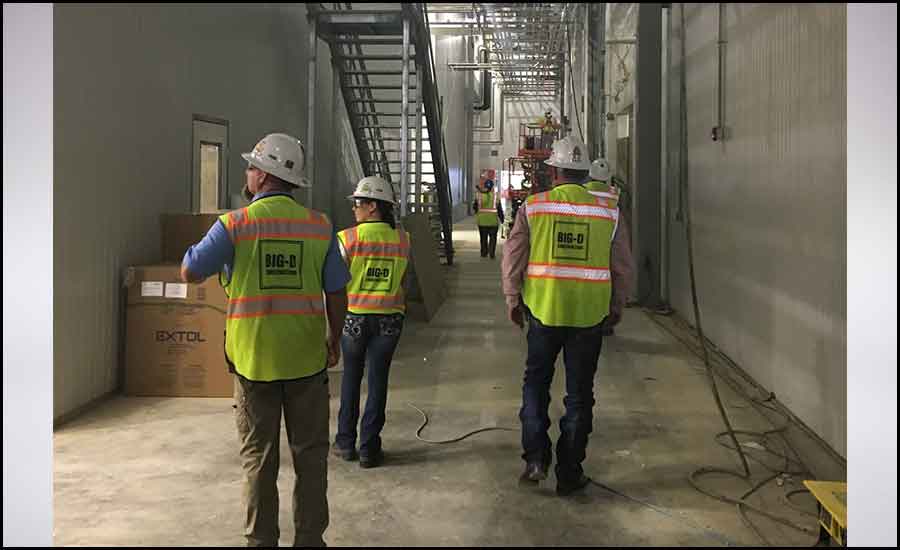
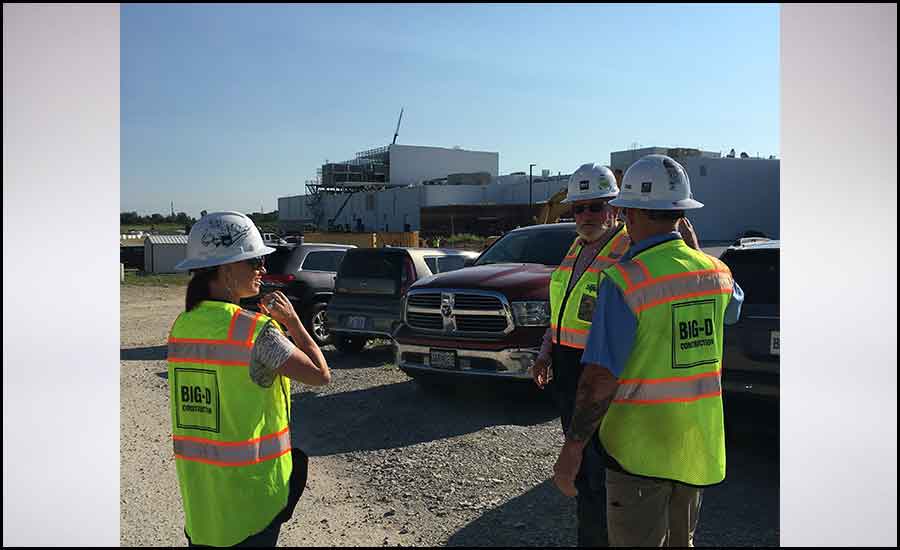
Site logistics for a renovation include working around existing operations indoors and with regular traffic and space limits for equipment and materials outdoors. Photos courtesy of Big-D Construction.
Boone adds that even with the extra hurdles, companies that opt for facility renovations are seeing less downtime, safer work environments, fewer injuries, happier employees, and lower turnover. “In several cases we’ve also helped clients design flexibility into their facilities to allow for faster expansion and growth in the future.”