Companies need their supply chains to be flexible, accurate and nimble to increase productivity and drive efficiency. Consumer expectations for speed, coupled with labor challenges, have companies across the cold foods spectrum looking to automation to supercharge their supply chain. Artificial intelligence technologies are pushing robots to higher levels of sophistication, machines are picking and packing orders, and IoT is improving the precision and mobility of equipment. But before adopting automation in the cold foods supply chain, it’s important to understand how these high-tech systems can be implemented and what they mean for the packaging used to transfer, store and organize product loads.
Automation Supports Operation
With e-commerce food sales growing, the efficient and safe movement of cold foods supply chain products is imperative. That’s where automated systems and processes can come in to help streamline operations at many points in the supply chain. In the manufacturing and production facility, automated systems from simple conveyors to complex robots are used to increase capacity, protect employees and improve quality and repeatability. For example, automated stackers and pickers can be used to move pallets throughout a complex racking network, helping to reduce picking errors and labor needs while improving warehouse capacity and productivity.
In the warehouse, the type of automation used varies from relatively simple to quite complex. Basic automation uses machinery and vehicles to increase pick rates per associate. Advanced systems take advantage of artificial intelligence and robots. For example, retailers can use conveyors, sortation systems and more to ensure fast, accurate order fulfillment. Automated quality control can be the answer for companies with a need for faster and more accurate fulfillment. Utilizing a series of scanners and cameras to assess products and determine if quality is acceptable, these technologies help to identify and resolve food safety, product integrity and traceability issues with efficiency and precision.
And in brick-and-mortar retail, automation is being introduced to help reshape the way employees work. The rise of micro-fulfillment centers also is reshaping supply chains, as small-scale automated storage and retrieval systems (AS/RS) can be used to help retailers store and retrieve product and inventory on demand to fulfill orders closer to the consumer.
Overall, the use of automation is growing at every level of the cold foods supply chain. And regardless of the type of technology being used, packaging is an important consideration — as it determines how efficiently an operation can transfer, store and organize product loads in these automated systems.
Choosing the Right Packaging
Rising customer demands in today’s food supply chain have companies looking to their packaging to improve the way they store, manage, retrieve and distribute product. And choosing the right packaging solution is a critical element in the design of an automated system. This is because packaging must seamlessly interface with these systems so it does not cause any downtime or any potential product damage.
When selecting packaging, companies should evaluate their supply chains by using these three considerations:
- Understand how reusable packaging fits in with current and future plans to adopt automation.
- Assess the different packaging options and how they support your company’s sustainability goals.
- Realize pain points in your operation when it comes to packaging and where there are opportunities to implement more sustainable and durable solutions.
With these considerations in mind, companies often choose reusable plastic packaging solutions due to their durability, reliability and sustainable advantages.
Plastic Plays a Role
Long before the boom in the adoption of automated systems, reusable packaging has played a leading role in ensuring seamless handling. Many of these benefits extend from the all-plastic construction of reusable packaging.
- Increased hygienics: With an increased focus on hygienics across the supply chain, the nonporous and flow-through design of reusable plastic packaging allows companies to easily sanitize their packaging for reuse. These solutions also can use FDA-compliant materials, adding to their food safety benefits.
- Repeat performance: The tight and consistent dimensions that plastic provides help ensure packaging interfaces seamlessly with a variety of automated systems to reduce downtime. This reliability ensures systems run more efficiently and products get into the hands of consumers as quickly as possible.
- Reduced slippage: One consideration in a cold storage environment is slippage. Frictional elements, grommets or molded in texture are all features of reusable plastic pallets that help to address these concerns.
Other advantages of plastic include the ability to incorporate more-detailed features, ergonomic features like handholds, durability for a long useful life and more. Overall, reusable plastic packaging helps to support the entire supply chain and offer logistics savings, faster pick times and accelerated fulfillment.
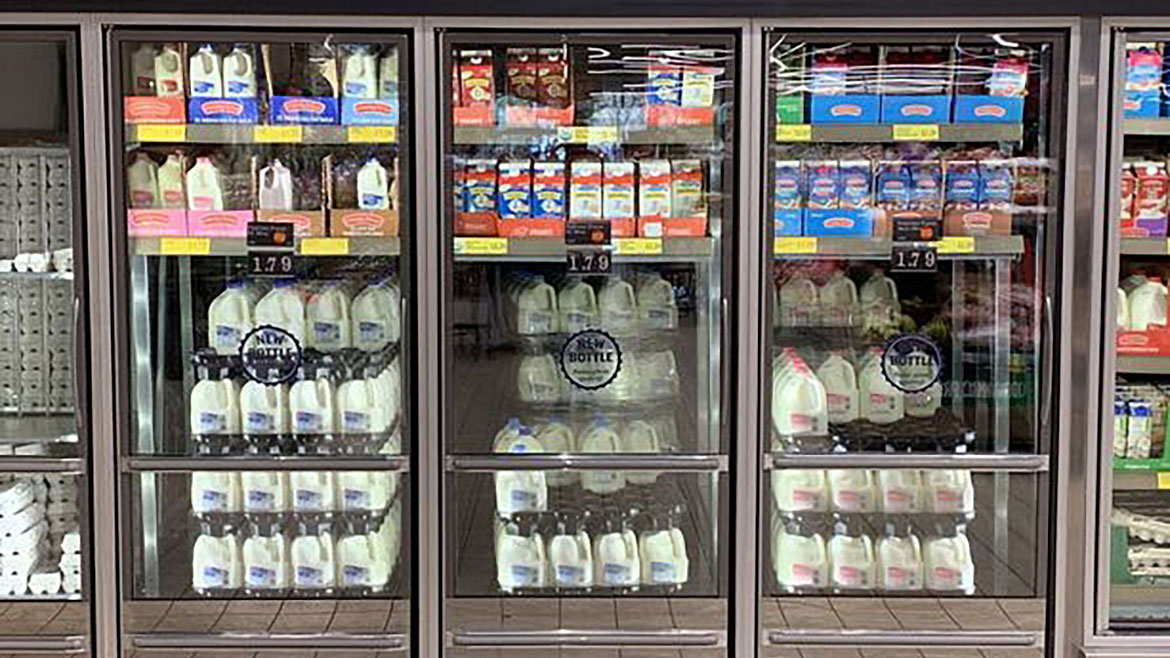
Packaging for Every Operation
Depending on the product being transported and the automated system being used, companies can adopt a variety of reusable packaging product types.
Reusable plastic pallets are a durable and impact-resistant solution fit for a variety of automated environments. The durability and life cycle of packaging products are key considerations for automated supply chains, and reusable plastic pallets make many trips through the supply chain before being recycled — which represents great savings over wood pallets on a cost-per-trip basis. In eliminating wood pallets, operations also reduce waste.
Given their all-plastic construction, these pallets are optimized for automation, as they are dimensionally consistent, which creates a smooth interface between automated systems and product loads. Features like steel reinforcements and frictional elements can be incorporated to further optimize pallets in the cold foods supply chain. These anti-slip pallet features help keep loads securely in place and reduce the risk of load damage during shipping and transit on material handling equipment.
Reusable plastic containers provide an alternative to corrugated boxes or cases to protect products in transit and improve efficiency throughout the supply chain. Unlike corrugated boxes or cases, reusable plastic totes and containers provide reliability in automated systems due to their dimensional consistency, have associate-friendly features like ergonomic handholds, and can be used for many cycles in the supply chain.
Certain reusable containers can also be designed to meet the specific system requirements of mini-load and AS/RS, as well as system integrator requirements. Other containers can support split-case picking, and containers with an attached lid can be used for easy transportation from the distribution center to the refrigerator case.
Stackable and collapsible bulk solutions are a lightweight and durable solution for automated systems and can be used for larger and bulkier items. Unlike cardboard boxes that must sit on a pallet with no attachment, bulk systems are integrated with a pallet to provide added stability that reduces the risk of shifting and damage through an automated system. What’s more, different bottom configurations allow flexibility with automation throughout the supply chain.
It’s important for companies beginning to adopt automated systems to work alongside both their automation and packaging providers to ensure their packaging meets system requirements.
Overall, automation continues to rise in today’s cold foods supply chain warehouses to optimize labor operations in low-temperature environments. It’s important for companies in the cold foods supply chain to continue to adapt and work through this new wave of automation. And with standardized and precisely molded reusable plastic packaging, companies can drive repeatable performance, help automated systems run seamlessly and prevent system downtime.