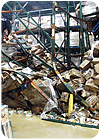
Photo coutesy of Frazier Industrial
It’s a business owner-operator’s worst nightmare: a complete warehouse rack system failure causing extensive product breakage, equipment damage, lost productivity and - far worse - worker injury or death.
Unfortunately, warehouse rack collapses - whether due to design and product inefficiencies or system misuse - are on the rise. Contributing to this is the prevalence of taller systems, installation of used racking, rack damage, use of improper lift equipment, system overloading and insufficient forklift training.
Fortunately, you can prevent a catastrophic rack collapse by understanding the causes of rack failure and by practicing proper inspection and maintenance.
Understand the causes
Warehouse operators need to thoroughly understand the causes of collapse as well as the primary sources of responsibility. This is important because major system errors can begin early in the project in the hands of systems designers, manufacturers or distributors.Errors and inefficiencies can creep in when there’s any miscommunication about the system parameters, improper system design and/or incorrect lift truck clearances.
It’s particularly important in this early stage that operators not sacrifice rack capacity for price reduction. This frequent, undesirable practice removes material steel from the rack design to simply cut costs. This approach not only results in an inferior design but also could lead to component failure.
Several of these same errors may occur at the rack manufacturing level - whether it’s improper system design or someone misinterpreting the design criteria. There also might be poor manufacturing practices - involving insufficient welding practices, component fabrication or quality assurance measures.
Of course, warehouse owners and managers shoulder a major responsibility for rack system success or failure. The nine most common failure issues include:
1. Rack damage– Lift equipment abuse is the leading cause of rack system failure and collapse.
2. Incorrect load weight – Overloading the rack system beyond its engineered weight capacity can result in component failure and ultimate collapse.
3. Altered configuration – Rack system configuration (shelf beam levels, bracing pattern, etc.) is carefully engineered to satisfy a customer’s operational requirements. Changes in shelf elevation, for example, can reduce column capacity and lead to system failure.
4. Lack of driver training – Improper lift equipment training is the leading cause of rack damage.
5. Change in operation – Misuse often occurs when business requirements mandate a new operational procedure.
6. Incorrect equipment use or change – Rack systems are designed for integration with specified lift equipment. An equipment change can result in unforeseen misuse and rack damage. For example, using standard fork trucks or pallet jacks in a Very Narrow Aisle (VNA) / wire-guided system will cause damage in areas where abuse-resistant measures don’t exist.
7. Reduced rack capacity for cost savings – Warehouse owners and managers may choose to understate actual capacity requirements in order to reduce rack equipment costs. This is a huge, dangerous mistake.
8. Used equipment – Used equipment might save money but it also puts your storage operation at risk. There is no means for design and capacity verification and all prior damage is inherited.
9. Mixed components from various manufacturers – There’s no assurance that a combination of manufacturers’ components will perform to original system design specifications.
Take responsibility, control
If your storage rack system is in jeopardy of failure or collapse, there are four steps you can use to reduce risk and ensure rack safety.The first step is to conduct a thorough rack safety audit. This means you’ll need to locate initial design drawings and calculations, document current elevations and rack layout, determine if the current configuration is structurally sound, examine the full extent of existing rack damage and plan to repair or replace your racks.
It’s important to keep a set of drawings reflecting your current rack configuration. This is a requirement of the Rack Manufacturer’s Institute (RMI) as well as the Canadian Standards Association (CSA).
The next safety step requires that you develop a driver-training program with accountability written into that process. It’s also recommended that you establish an on-going rack safety audit program and that you install and maintain rack capacity plaques in several obvious and clearly visible locations.
Ongoing maintenance
The proper rack maintenance program not only reduces the risk of rack failure but also extends rack system life.Operators start by simply developing a schedule for periodic rack inspections. Inspectors should report all damage to management. Likewise, it’s important to develop repair criteria for damage. This means that your employees note the severity of damage and understand the required repair procedures.
It is highly recommended that operators not use repair kits other than those approved by the original rack manufacturer. A bracing system repair must be consistent with the original frame design.
Lastly, we recommend that warehouses develop a comprehensive forklift training program for all new operators.
Carlos Oliver is president of Frazier Industrial, a Long Valley, N.J., rack manufacturer. The preceding text was excerpted from Oliver’s presentation to the International Association of Refrigerated Warehouses.
Want to learn more?
Frazier’s Rack 101: How to Design Your Pallet Rack System.Frazier Industrial offers a fully illustrated 28-page manual with step-by-step instructions and diagrams to help warehouse owners design a safe pallet system. Call (800) 614-4162 or visitwww.frazier.comfor details.
Rack Manufacturers Institute (RMI):
Formed in 1958, RMI represents all major U.S. rack system manufacturers. RMI’s goal is to advance standards, quality and safety for the intended use of industrial steel storage rack systems and research rack structures through testing. In regard to rack safety, RMI has developed a specification for design, testing and utilization of industrial storage racks. This guideline addresses conditions unique to material handling environments that can affect rack stability (fork truck abuse, rack loading and unloading). The complete specification may be downloaded from RMI’s website atwww.mhia.org/industrygroups/rmi.