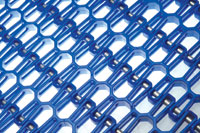
Processors can use every advantage they can get. That said, Ashworth Bros. Inc., Winchester, Va., believes that the unique design and construction of its new Advantage conveyor belt delivers greater energy savings and production throughput.
To back up its claim, Ashworth commissioned Intertek ETL Testing Services (ETL) to conduct comparative air flow tests and quantify air pressure drop (air flow resistance) of all commonly available plastic spiral belts.
The results were clear.
“ETL’s testing proved that Advantage belts perform with up to 370 percent less pressure drop than the leading competitors’ plastic belts,” Ashworth says. “The lower air pressure drop increases a spiral system’s overall efficiency. More air flow decreases dwell times, which increases production. Less air resistance increases the efficiency of evaporator fans and this lowers electric consumption.”
Ashworth says its Advantage belting uses stainless steel rods (instead of pliable plastic rods) for the strength needed to increase the open area of the plastic mesh. In addition to increasing air flow efficiency, the Advantage belt’s design improves its cleaning characteristics.
Ashworth notes that Advantage belts are the only plastic spiral belts accepted and/or approved by USDA, NSF and BISSC for cleanable performance. Company officials add that the stainless steel rods resolve other common problems inherent to plastic rod belts. Beam strength is increased allowing the Advantage belt to support heavier loads without sagging; plus, less support rails are needed for wider belts. This also reduces friction and saves energy.
Ashworth says its Advantage 200 & 120 belts are available in from 1.5 turn radius and larger and are designed to operate in harsh environments as low as -50F(40°C) or as high as 180F(82°C). They are rated to withstand 300 pounds of tension at 100,000 cycles.