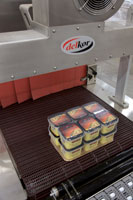
That’s because this is prime selling season for D&D, a refrigerated deli salad processor in Omaha, Neb. A wholly owned subsidiary of the Hy-Vee Inc. supermarket chain, D&D produces more than 250 bulk and ready-to-eat refrigerated deli products for 229 Hy-Vee stores in an eight-state region.
D&D’s 90,000-square-foot plant processes, packages and ships its foods in plastic buckets, bag-in-box containers and in mold labeled containers. Wallace says D&D has two automated filling lines dedicated to as many as 23 SKUs ranging in size from 7 ounces to 16 ounces. Bottom line: it’s all about production volume.
But the big numbers don’t stop there. This summer finds Wallace excited about even more facts and figures – related to labor and cost savings. That’s because D&D installed automated, end-of-line packaging equipment from Delkor Systems Inc., Circle Pines, Minn.
Delkor’s Spot-Pak System is a fully automatic, end-of-line packer engineered to handle a wide range of product sizes and pack patterns with tool-less changeover in just a few minutes. Spot-Pak is specifically designed to package product onto a flat, corrugated pad in lieu of traditional boxes with a substantial resulting reduction in corrugated usage.
Dale Andersen is Delkor Systems president.
“The net corrugated savings for D&D Foods was quite impressive – at approximately 70 percent compared with their previous corrugated case,” he says. “When you combine the dual benefit of a fully automatic packaging line with this level of packaging material efficiency, it can be very significant.”
Already widely popular in dairy applications, Delkor says Spot-Pak also is ideal for refrigerated deli salad processors.
It’s here that Wallace picks up the savings storyline.
“We are always looking at ways to take unneeded costs out of the system and get products to the stores at the lowest possible costs,” he says. “Most Hy-Vee stores already do a great job with recycling – so reducing the cardboard in our packaging seemed like a natural fit.
“We have experienced various peaks and valleys in the cost of corrugated over the past few years,” he continues. “Our business plans shows that we can reduce our exiting packaging costs by almost $75,000 annually with this first phase [operations change] and this does not count the labor or fuel savings when shipping the cardboard.”
Another important savings area? Labor.
“Before, our employees would hand pack our finished retail containers into corrugated boxes – and then run those through automatic tapers,” says Wallace. “We also looked at the potential labor savings [offered by Spot-Pak] as well as the need to avoid any employee repetitive motion injuries.”
Although D&D considered other options, Wallace says it was a 2009 trip to another Delkor customer that sold him on the Spot-Pak machine. D&D then arranged last winter (during its slow season) to install the line and have Delkor train D&D workers.
Today, Wallace is a convinced customer.
“Delkor has been a great business partner with us and has already shown how their customer service works,” he says. “We had a heater module go out on the July 4th weekend and they were great at getting a part to ship to us so we were up and running the following Tuesday morning.
“There always is a learning curve with new equipment or a change in production procedures,” he concludes. “This change created a few learning curves but D&D believes this was the right decision. We expect it to pay economic and environmental rewards for years.” – Delkor Systems Inc.
(800) 328-5558 / www.delkorsystems.com