The ongoing labor crisis along the cold chain has necessitated a number of changes throughout the industry to keep up with record demand for goods. Generous hiring packages might entice additional workers into the field as a short-term solution, but long-term solutions—particularly in cold storage and warehouse environments—likely lead to automation. In particular, using AGVs (automated guided vehicles) to do the difficult, repetitive work of loading, unloading, storing, and retrieving cold foods for distribution.
“With ongoing labor shortages, AGVs are an ideal way to fill the gaps in the workforce, and AGVs don’t experience the same physical hardships as human employees in cold storage with freezing temperatures,” says Derek Rickard, director of sales at Cimcorp. “When cold storage facilities leverage AGVs as part of a complete, end-to-end automated solution, human responsibilities can be shifted to supervisory tasks, such as picking sequence selection and maintenance. Staff will no longer need to brave the cold, creating significantly better working conditions to attract and retain new employees.”
For cold chain companies planning a new facility or to retrofit an existing one with AGV capabilities, Rickard and Ethan Kroh, project manager at ARCO National Construction, offer a few guidelines to maximize an AGV environment.
Put it in the Plan
Operators may waver on whether to invest upfront in AGV infrastructure for a new warehouse, especially when they’re already spending millions of dollars to construct a cold storage facility. While a building can almost always be adjusted later for AGV use, Kroh says there are many advantages to adding AGV plans to a structure’s blueprint.
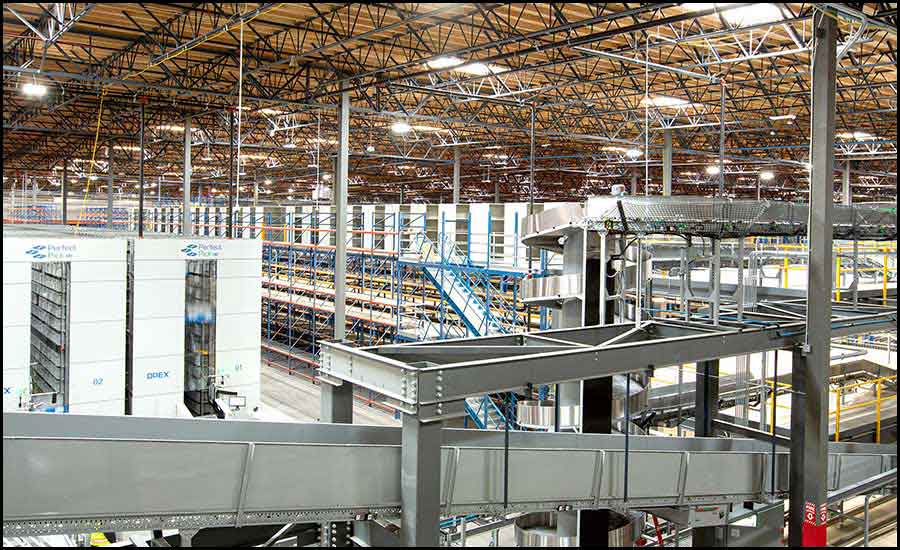
“More often than not, adjusting the initial design for construction will be more cost-effective than retrofitting a building in operation. Once the building is operational, activities that are not related to product movement are a hindrance,” he says. “With most equipment using a wire guidance system and storage heights increasing, special accommodations need to be accounted for in the slab capacity, rebar placement, and flatness tolerances. For radio-signaled equipment, product layout and signal coverage becomes a concern for connectivity. Making all of this work in a cold storage environment also adds to the design conversation for equipment capabilities at freezing temps or below.”
Rickard adds that, “extra expenses can be avoided by having specific locations planned for AGVs during the building process. The advantage of building new is that it presents an opportunity to design the most optimized layout considering inventory locations, corridor width, lifting heights, fire protocols, and communication interfaces, which can be more cost-efficient.”
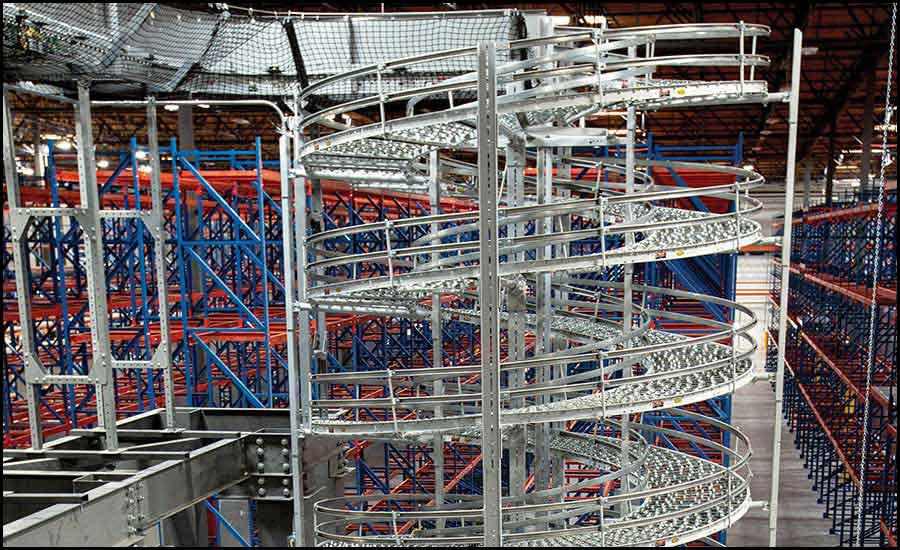
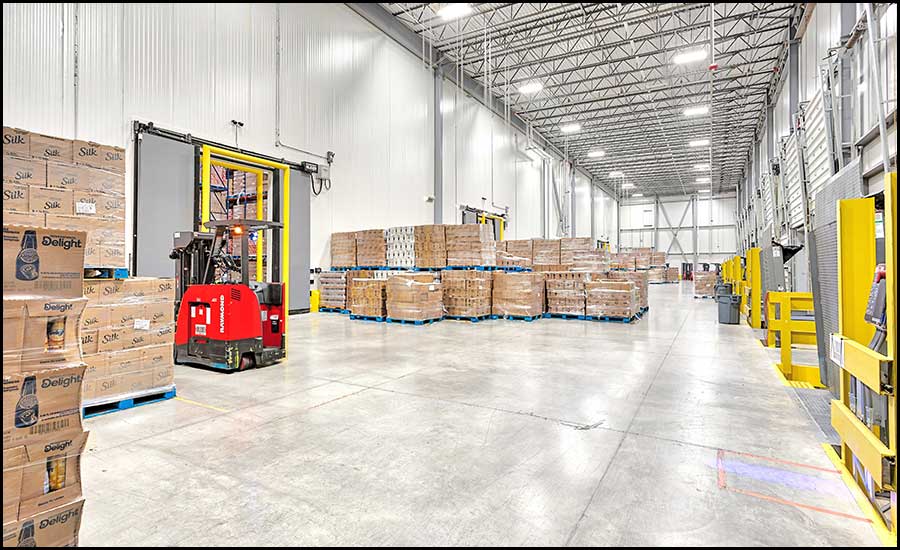
Retrofit Options
New-build warehouse design for AGVs may be preferable for the reasons noted above, but retrofitting an existing building with AGV capabilities is still a practical solution if operators accept the limits inherent in their facilities.
“With older buildings you may be implementing AGVs around existing limitations, such as ceiling heights, columns, employee work areas, and more,” notes Rickard. “An important thing to note about AGVs is they have the flexibility to fit easily within existing cold storage facilities. However, the cost to retrofit can vary greatly depending on warehouse size and many other factors. Pallet-handling, forklift-style AGVs are the most requested vehicles for retrofits. Lower lift AGVs have the ability to lift pallets 23 feet to go in a four-high pallet racking system, which is ideal for retrofitting into a standard facility. The high lift VNA—very narrow aisle—is often used for cold storage, as many cold facilities are designed with very high storage and narrow aisles.”
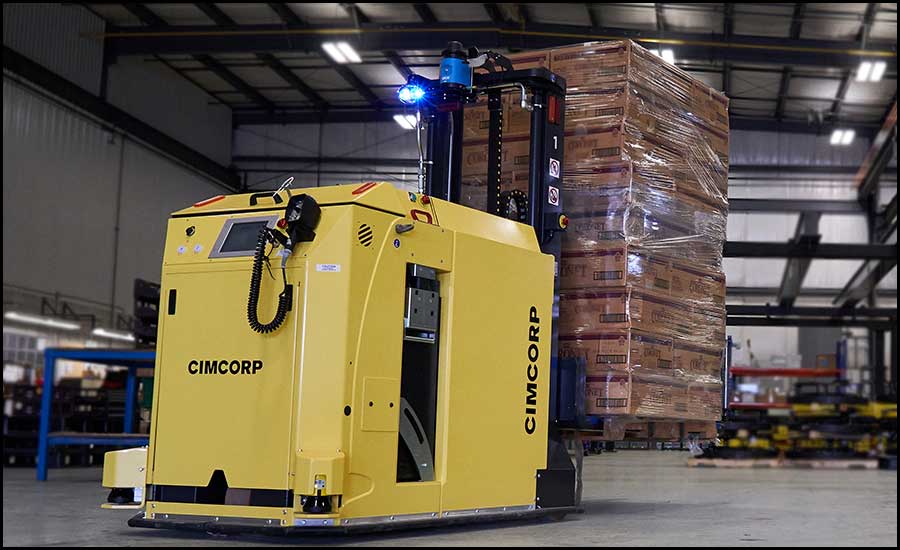
Room to Roam
Many of today’s advanced AGVs can quickly adapt to a number of different warehouse footprints, regardless of whether it’s a new-build or existing structure, reducing the learning curve for busy operations. “Many AGVs have the ability to map the production floor instead of using fixed magnetic tapes or reflectors to move around a facility. This open-path navigation ensures that any pathway to a desired destination is a viable option for the AGV. Couple this with built-in obstacle avoidance and you have an easy-to-implement solution,” Rickhard explains.
The actual space needed to store and charge AGVs in a facility doesn’t require much additional real estate either, according to Kroh. “Most AGVs can operate within a similar storage space when compared to non-automated applications,” he says. “You would have additional charging stations and maintenance areas for the more extensive equipment and electrical needs, but fewer employees due to increased automation would lead to a smaller office and wellness space. In my experience, I have not seen a drastic square footage adjustment for AGVs in warehousing versus non-automated.”
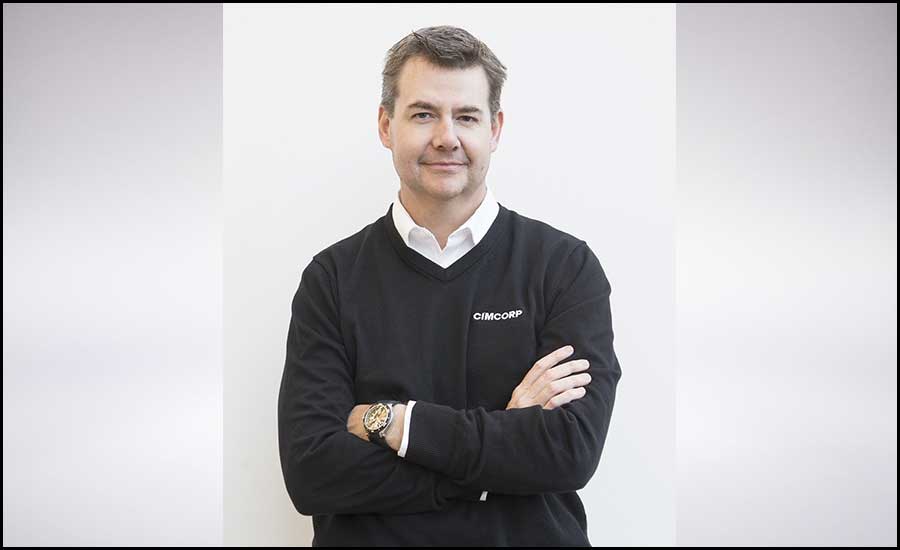
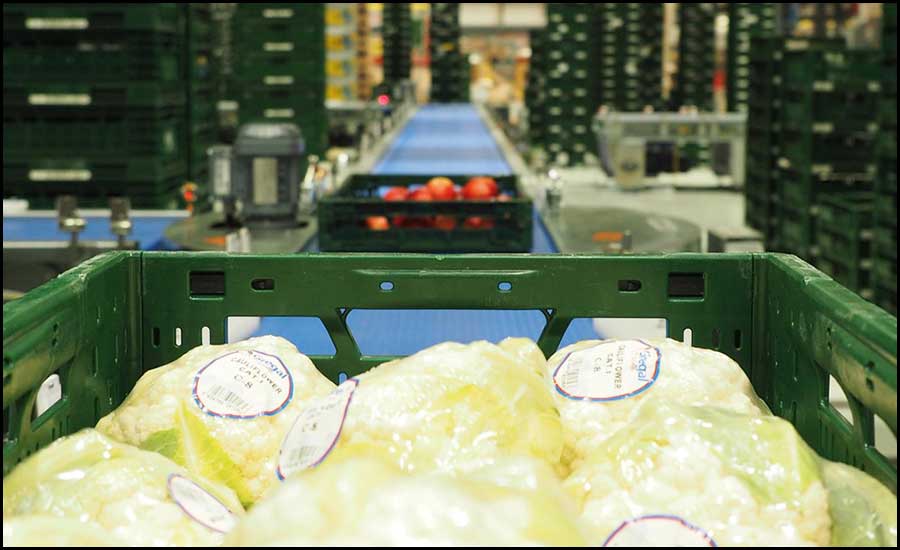
Cold Challenges
While AVG use is widespread throughout the supply chain today, cold foods facilities present several unique challenges for operating the vehicles. “Cold environments have an impact on hydraulic fluids and electronic components, and can present difficulties with laser-driven vehicles if frosting happens on reflectors. The good news is many AGV manufacturers consider these factors today, so before selecting an AGV vendor, be sure to check the capabilities of a vehicle in a cold environment to ensure it meets your needs,” says Rickard.
One true long-term benefit to utilizing AGVs in a cold facility aside from labor savings is they can generate a significant amount of statistics about the facility itself through telemetrics, and operators can use those numbers to apply efficiencies where needed—a valuable benefit as business along the cold chain continues to accelerate.
“As part of an automation package, companies are looking for analytics that gauge uptime and throughput—the average time per storage and retrieval,” Rickard says. “With activity reporting, they can better optimize the fast-moving products, relocating inventory for better throughput.”