With the pandemic easing, consumers and cold food processing providers have settled into a new normal. “New” applies to just about everything – what consumers are choosing to eat, how it’s being purchased and how it’s being distributed. Builders in the cold food processing space are meeting growing demands and there are no signs of it slowing down. According to MarketsandMarkets, the cold chain is expected to be valued at $10.2 billion by 2026. That’s up from $4.7 billion in 2021. Further, CRBE predicts the need for cold storage space to increase by 100 million square feet in the same time period.
Healthier Frozen Foods
Many consumers are shifting to a healthier lifestyle post-pandemic. A recent study by the American Frozen Food Institute (AFFI) indicates that many consumers are seeking a wider selection of frozen foods made with fewer, and more premium, ingredients, particularly with dairy and pet food clients. The AFFI study showed more than half of shoppers are purchasing more frozen foods, 58% are purchasing different kinds of frozen foods and 57% are purchasing different brands than they did pre-pandemic. This shift is a driver for the increase in cold storage demand and is expected to maintain pace through 2022.
Omnichannel Retail
Another focus among cold food processors is omnichannel retail. A seamless shopping experience through all available channels (in-store, curbside pick-up, home delivery, etc.) has shifted consumer expectations. Immediate access to goods, 24-hour responsiveness and the ability to purchase in “eaches” (individual amounts) is the norm.
The packaging and order fulfillment challenges that have resulted from this shift have pushed cold food processing providers to re-think their approach to food storage and logistics. Many are choosing to produce finished goods that can be shipped directly to retailers or even customers.
For example, some protein processing clients are adding blast freezers at their plants to eliminate the burden of transporting product off site to be frozen and packaged before reaching a distribution center. Onsite blast freezing makes them more agile and able to respond to the changing environment. In addition, many protein processers are improving value-added services be installing variable retention freezers (VRTs). The VRT improves case quality and allows for case selection at the plant.
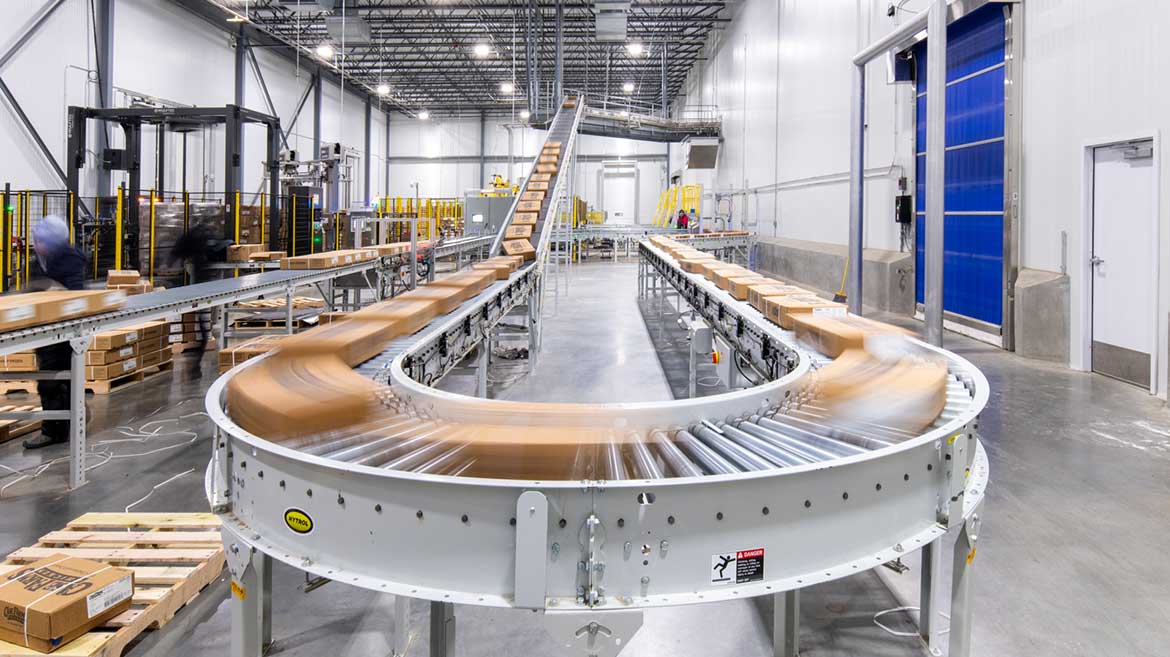
Labor Shortage
If you ask any cold food processing provider what their No.1 challenge is, their answer is almost always workforce retention. Labor has been a burning issue for over a decade: add to it the Great Resignation and you have an industry in need of a new approach.
Automation is key. In the past, owners justified automation costs against existing labor. Now, with a diminishing labor pool, owners view automation as an essential element to sustaining the supply chain.
Automation trends that have been to be successful for cold food processing providers tackling the labor shortage include:
- Automated Storage & Retrieval Systems: Automatically retrieve stored products.
- Automated Guided Vehicles (AGVs): Driverless vehicles to move product through a plant.
- Palletizers & De-Palletizers: Stack or remove cases on pallets.
- Automated Packaging, Labeling & Wrapping: The last step in preparing finished goods for direct shipment to retailers or consumers.
These solutions move product efficiently and safely through the plant and allow for a more flexible, coordinated and trackable product flow.
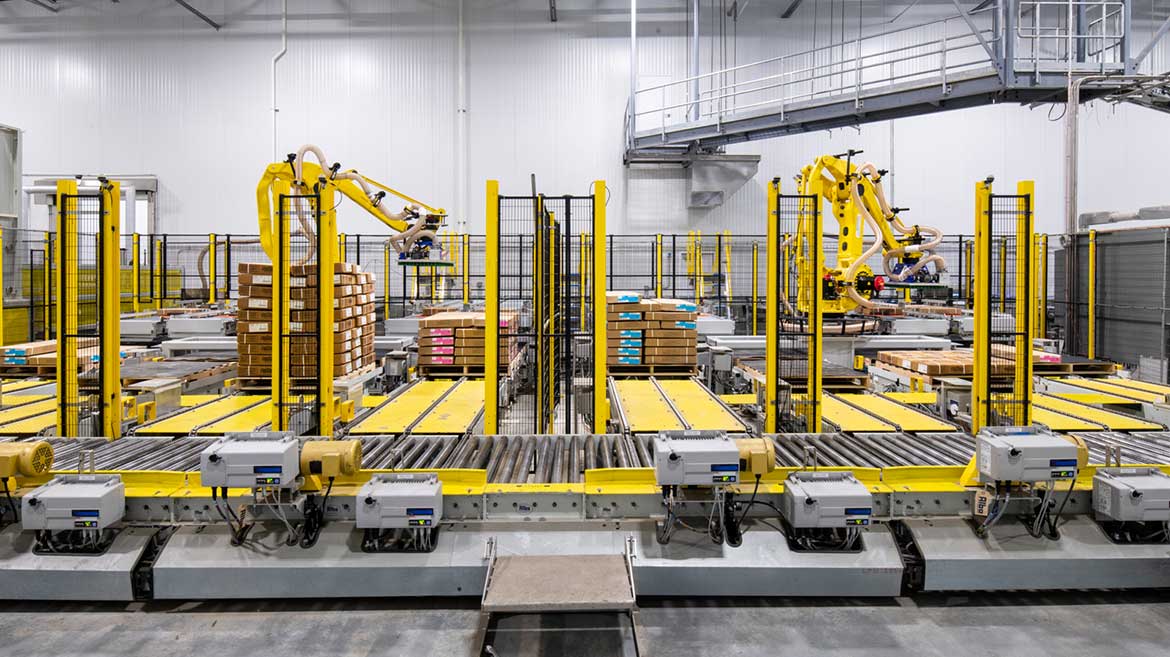
Warehouse Management Systems (WMS)
A WMS is software used to manage warehouse operations. While this technology has been around for years, new adaptions include the ability to connect with onsite automation equipment and implement algorithms that automate functions and gather data.
Implementing WMS software is an expensive and long-term commitment but many firms have in-house experts providing consulting services to minimize challenges like under-utilizing features, missing or duplicating essential steps, or not understanding how software can connect. The goal is to help customers have a clear view into their operations and make informed decisions about production, which is crucial for optimization. Additional benefits include better inventory management, reduced human error, cost and space efficiencies and faster order fulfillment.
Digital Supply Chain
The Internet of Things (IoT) is rapidly changing supply chain management. Cold food processing providers have access to more data from more devices and software than ever before. This information has the potential to form an integrated network that gives owners a global view of inventory in real time. Augmented reality, artificial intelligence and machine learning are all on the horizon and expected to result in better decision making throughout the supply chain, from inventory and intralogistics to weather and delivery routes.

Carbon Neutrality
A study by Gartner, a technological research and consulting firm, found 85% of investors value environmental, social and governance criteria when making investments. This trend has pushed cold food processing providers to explore carbon neutrality as a way of engaging stakeholders. Carbon neutrality (or net zero carbon) encourages owners to change their behavior on high-emission activities. They can also offset emissions generated by their facilities by reducing them elsewhere. Carbon neutrality builds off the foundation put in place by the U.S. Green Building Council, which has been an industry standard for over a decade.
By keeping on top of these industry trends, cold food processors can overcome disruption and remain competitive in 2022 and beyond.