National security evokes discussions and legislation aimed at America’s physical borders, financial or energy infrastructure but a critical – and often overlooked – piece of any country’s national security is the safety and availability of its food supply. To the extent our nation’s food supply is in jeopardy, whether raw agricultural ingredients or processed foods, the country can find itself in deep peril. The importance of cold storage real estate for U.S. food security cannot be overstated. The decisions food supply chain managers make today can affect the food supply of Americans for generations to come.
By the 1970s, the U.S. became the world’s largest food exporter. This was a significant and consequential shift, as prior to that time the country had been a net importer of food. Previously a liability that exposed the country to food supply risk, food production has become a significant portion of America’s gross domestic product (GDP), representing over 5%, with exports totaling $196 billion in 2022, according to the U.S. Department of Agriculture (USDA).
Advances in technology and transportation, allowing for more efficient and cost-effective production and distribution of food, drove America’s increased food export business. Through the tireless efforts of American farmers (97% of all U.S. farms are family-owned and operated), food researchers and manufacturers, the country’s food supply has surpassed the requirements of our family’s dinner tables. Cold storage plays a critical role in the food supply chain, providing a place to store perishable food products before they are transported to retail and restaurant outlets, and ultimately, to consumers. Unlike America’s extraordinary ability to produce food, our ability to store this vital resource has not been as robust.
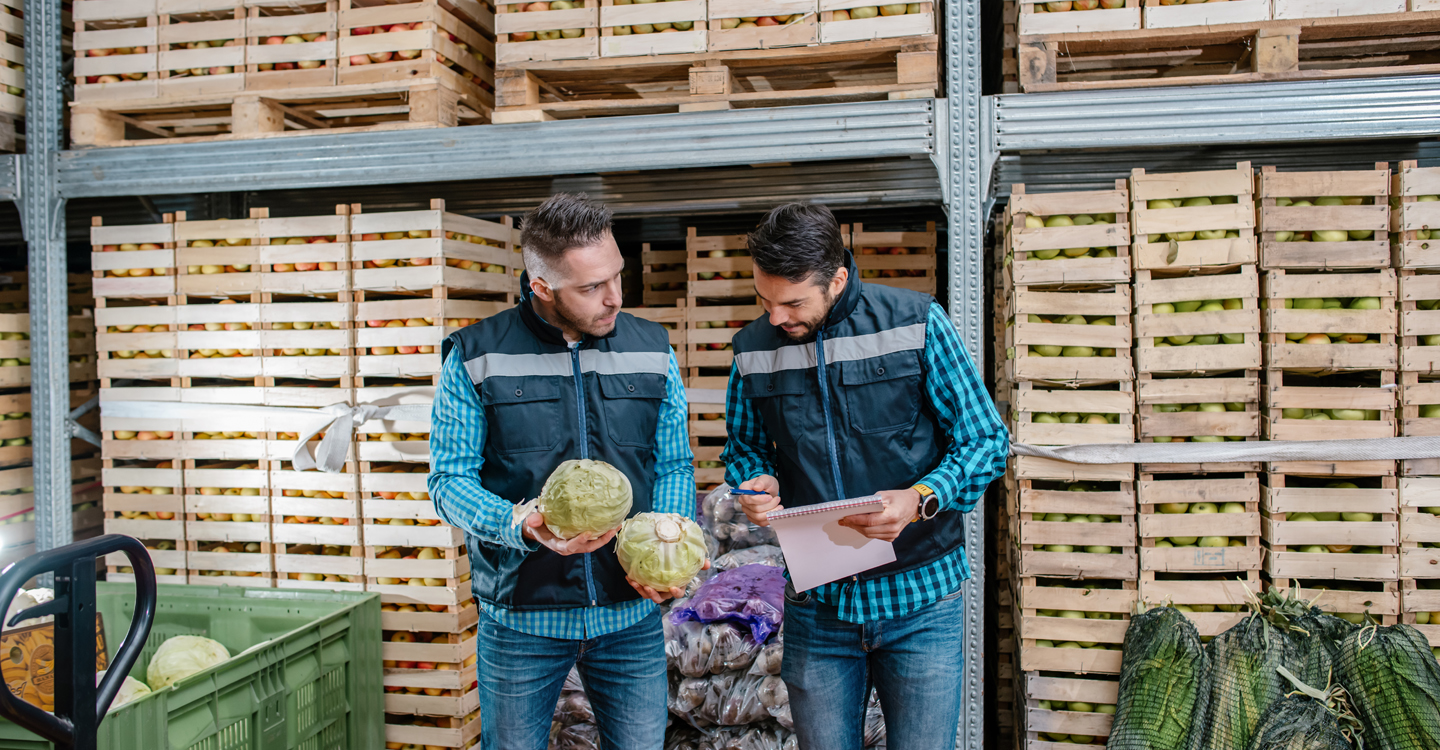
It has been estimated that there is roughly 200-million square feet of unmet cold storage demand in the U.S. E-commerce is expected to climb to 21.5% of all grocery sales by 2025, driving demand for cold storage, particularly in grocery and DTC. According to national real estate firm CBRE, there was over 3.3 million square feet of speculative cold storage development under construction in 2022, up from just 300,000 square feet in 2019. Development of new cold storage has struggled to keep pace with consumer trends, as construction and land prices have regulated how few buildings can be built. Meanwhile, existing facilities are beginning to be operationally obsolete with the average age of existing cold storage being about 40 years old. This demand results in an incredibly low vacancy rate, making finding space difficult for some of the biggest food manufacturers and distributors, and startup food companies alike.
Indeed, so finely tuned is the current network of cold storage warehouses and the food supply chain, that one hiccup in the supply chain can cascade throughout the country. The closure of a Smithfield Foods plant in Sioux Falls, South Dakota, in April, 2020, due to COVID-19 outbreaks highlighted the critical importance of cold storage real estate to the country’s food supply. The plant, one of the largest pork processing facilities in the U.S., processed up to 5% of the country's pork supply and the plant’s closure resulted in a significant disruption and pork shortages in some areas of the country.
As a result, Retailers and distributors struggled to find alternative sources of pork and protein products and consumers were left holding the bag. There simply wasn’t enough supplementary protein inventory stored in the chain to alleviate demand pressures. The result? Quantity limits and store-mandated purchasing controls of all proteins at nearly every retail outlet for months.
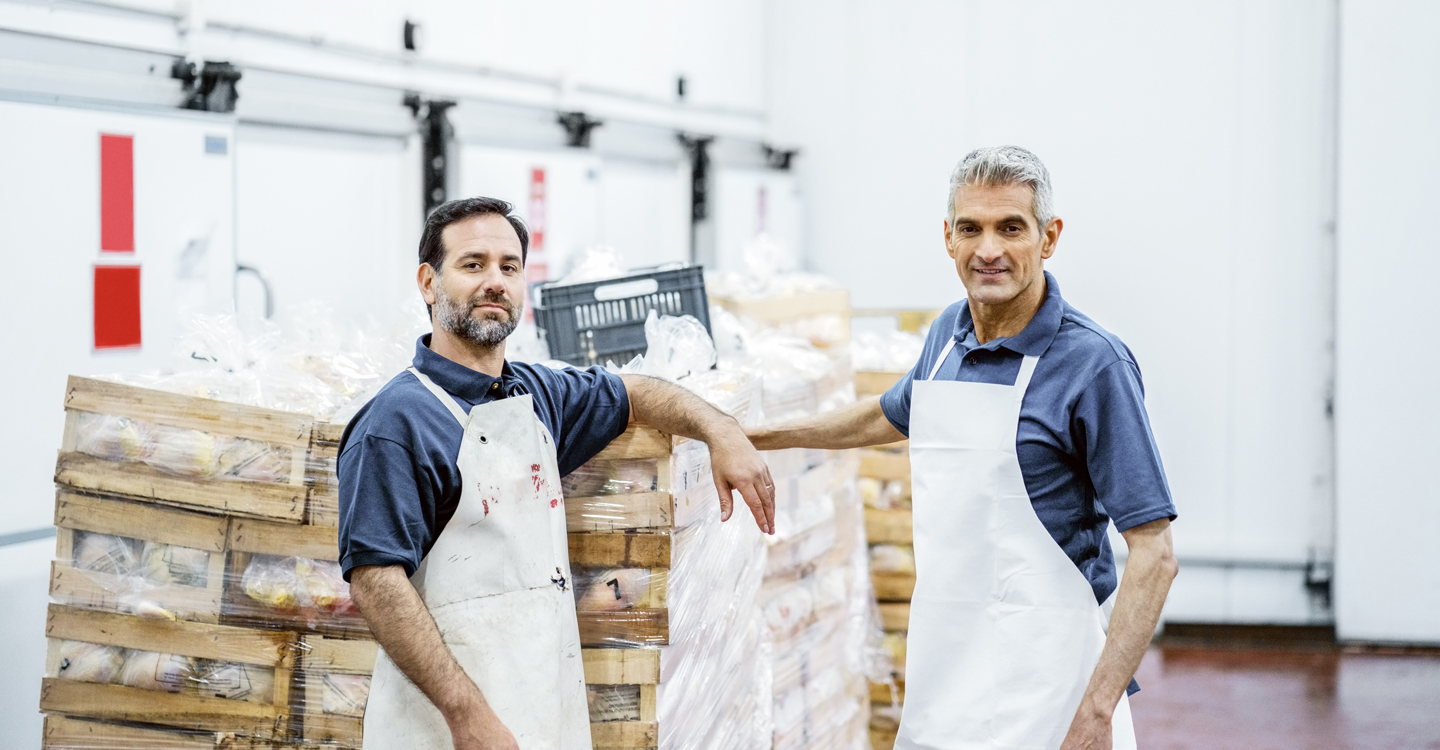
If you are a food processor or manufacturer, this lack of redundancy should come as no surprise. As supply chain directors at our nation’s food manufacturers doggedly work to procure space, it seems like there is never enough. Further, fees for food storage and handling continue to rise as warehouses demand a premium for what little space is available. These price increases, coupled with commodity inflation, is straining the underlying consumer.
R&FF’s new special content project, Farm to Frozen: Navigating the U.S. Cold Storage Climate, will focus on the cold storage market, the growing need for infrastructure development and how food and beverage manufacturers/processors can leverage the best options to fit their unique needs.
Throughout this continuing multimedia series, we will explore every option available to food manufacturers and processors for acquiring new space, new ideas like creating bidding environments between 3PLs, using tax and economic incentives and more. We’ll cover every approach from do-it-yourself to complete outsourcing and everything in between as a real estate primer for food supply chain professionals.
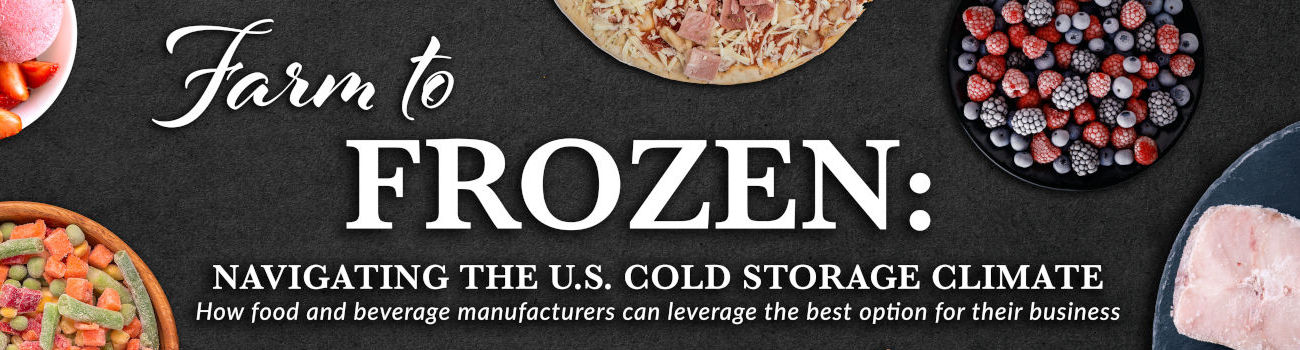
Would you like to be alerted when new Farm to Frozen articles are posted?
Sign up to receive our eNewsletter, What's HOT in COLD! This weekly eNewsletter showcases the latest trends, news technologies and products impacting the refrigerated, chilled and frozen segment. It also includes a notice when new Farm to Frozen content drops! Sign up now to get on the list!