Demand for cold storage is soaring in Space City.
“The Houston market has been experiencing record import levels as companies look to Houston for relief from congestion at the ports on the East and West coasts,” said Brian Beattie, president of Western U.S. Operations at Lineage Logistics. “Houston is a fantastic location for companies looking to provide an alternative entry point from the busy ports on the East and West coasts. It has an overweight corridor that allows importers and exporters to load up to 60,000 pounds of cargo on containers and move them with a 30-mile radius of the port. Equally important, companies in our industry are finding that placing product in Houston can service the majority of the country within 24-48 hours.”
Lineage has 130,000 pallet positions across five Houston sites, are each less than 10 miles from the port and are within the overweight corridor. In addition the company can leverage 14 additional locations across the state of Texas, including the Dallas/Fort Worth and San Antonio metro markets, Beattie said.
Houston is a port-focused market: for example the movement of U.S. poultry, beef, and pork totaled a half-billion dollars in 2021 and demand is projected to increase.
The U.S. Department of Agriculture (USDA) last year announced a partnership with the Port of Houston to address supply chain challenges and improve service for shippers of U.S.-grown agricultural commodities. However, limited availability of equipment, specifically chassis, at the port to move and position reefer containers risks the loss of millions in additional sales and would have broader impacts across the food supply chain. Without action, these challenges would threaten the ability of the poultry and meat industry to effectively continue exporting from the port Houston, adding to the strain of already congested other ports.
“Port congestion was a big challenge for the Houston market this year. There was simply more container volume arriving into the port than the existing infrastructure and support services like container chassis and gensets could effectively handle. This resulted in high demurrage, per-diem and other fees incurred by importers,” Beattie said. “Also, vessel schedules have been erratic, which caused missed bookings and impacted export schedules and timing. Many protein exporters prefer to ship product from inland locations and have that product ship out within one to two weeks upon arrival at the port based facility. When we miss a booking, and our facilities are at capacity, it causes the whole system to get backed up. This creates a situation where the protein company has to find alternative storage locations near the processing locations and then ship to the port facility when space becomes available.”
With more perishables moving through southern ports, strong growth in food sales and an insufficient and aging stock of food storage facilities, several cold storage projects opened in the last year. The most recent of which is Blackline Cold Storage’s 298,000-square-foot cold storage facility at the Port of Houston.
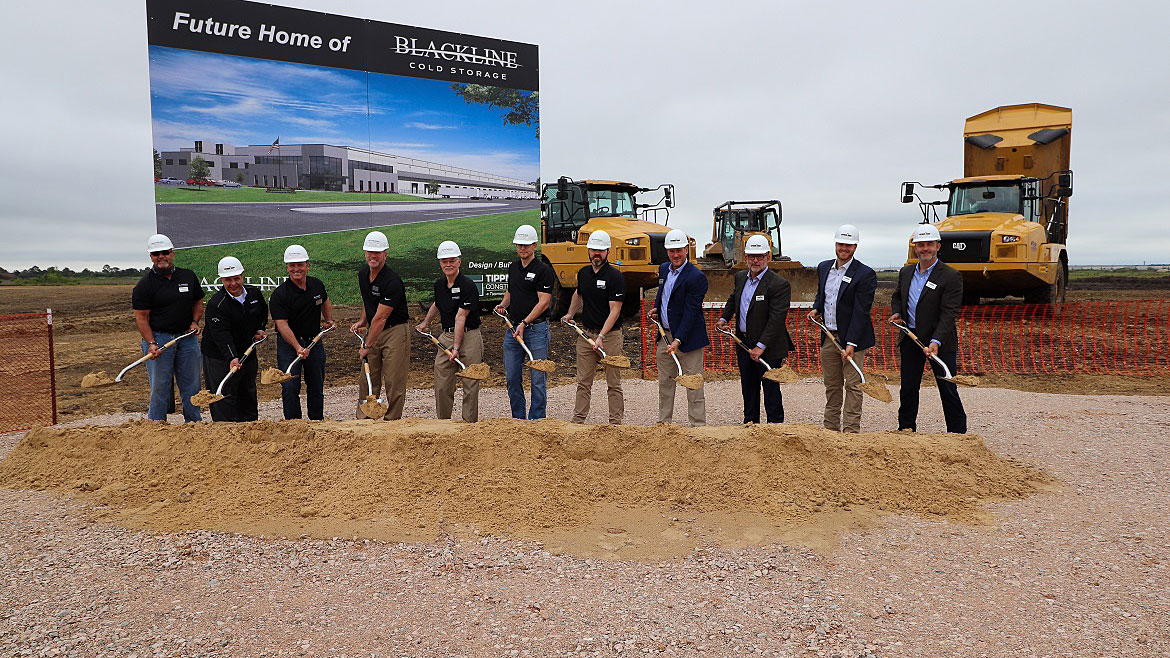
The facility is located within the heavy-haul corridor, in close proximity to the Barbours Cut and Bayport container terminals, and with convenient access to the regional interstate highway system and multiple Class 1 railroads.
The Tippmann Group designed the building to incorporate flexibility for multiple segregated temperature zones (including blast freezing capability), 48-foot ceiling heights, up to 50 truck doors and rail connectivity in order to serve a broad range of customer requirements. Blackline selected Ryder to manage the facility's warehouse operations, scheduling, order fulfillment and distribution services.
Houston ColdPort, a 315,101-square-foot speculative cold storage warehouse opened last summer. The site features a 50-foot clear height warehouse, a 60-foot-deep cold dock, 38 dock positions with vertical storing hydraulic dock leveler equipment, LED lighting throughout, a 200-foot-deep truck court with 57 trailer parking spaces and ample automobile parking. Located at the northwest corner of Beltway 8 and U.S. Route 90, the site provides access to major U.S. east-west and north-south thoroughfares – Beltway 8, U.S. Route 90, Interstates 10 and 69.
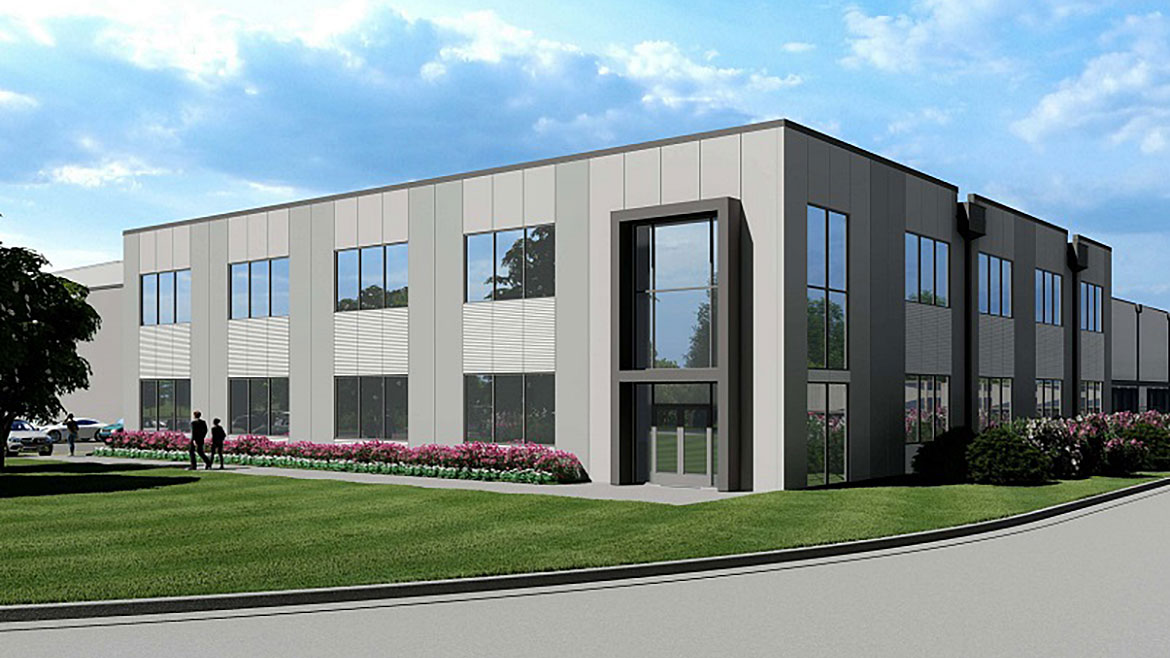
Other recent projects include a new facility in 2020 designed by Houston-based KDW for whole and packaged beef, pork and poultry products for foodservice and restaurant operations. The 43,742-square-foot cold storage space was master planned with the ability to double its size for future needs.
The population of Texas is booming, with a 15.9% growth rate in the (2020) Census for a total population of 29 million and a projected population of over 31 million by 2050.
Houston ranks No. 14 out of the country’s top 80 real estate markets list from the Urban Land Institute and PwC. That ranking is up 10 spots from last year’s list, with Houston being a market where “the convergence of science and technology is happening within innovation communities” and the “long-term view on the life sciences sector is quite positive,” according to the report. Non-residential construction activity increased over 34% in the most recent three months compared to 2021, and the region is benefitting from increases in warehouse and manufacturing construction.
“The need for cold storage in Houston is growing like crazy,” Mike Day, CEO of Blackline Cold Storage, said in a 2021 news release announcing the groundbreaking. “It’s driven by several different factors. The import/export trade through Port Houston is growing, and of course the port itself is growing, investing in major projects. There’s a big need for import export of all goods, including cold products.”