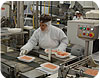
Butterball’s Mount Olive poultry plant processes more than 600 million pounds of turkey products a year.
As if being the nation’s largest turkey processing operation isn’t enough distinction, Butterball LLC’s Mount Olive, N.C., plant deserves attention for several other reasons.
One in particular, says Complex Manager Phil Paulk, is earning Rising Star Status from the North Carolina Department of Labor. State government officials only grant Rising Star status to facilities that pass a thorough Occupational Safety and Health Administration (OSHA) inspection and demonstrate a commitment to comprehensive health and safety for all employees, according to NC OSHA.
“Achieving this status has been a vision of the leadership group at the facility for several years,” Paulk says. “Our complex has always placed associate welfare in the forefront of all that we do. It took every associate in the plant - both hourly and salary - working together, focused on and committed to safety to achieve this recognition.”
Mount Olive’s achievement is made all the more impressive when the sheer size of the facility is taken into account. Just consider that last year more than 2,600 plant associates processed 145 million pounds of fully cooked poultry product and 476 million pounds of ready-to-cook poultry in the 650,000-square-foot facility.
“Operating the largest turkey processing facility in the world is a challenge,” Paulk acknowledges. “In order to continually improve, we must challenge each other and our processes daily.”
One way Mount Olive executives ensure that management stays challenged is a rigorous Leadership Training Program that requires plant leaders to complete 40 to 80 hours of training per year.
“To be successful we need to be certain everyone has both the skill and ability to perform their work,” Paulk says. “Training is constant and something we are very proud of. Our Leadership Training Program is world class and something we value.”
These training programs include classes ranging from HACCP reviews to associate welfare classes.
“I believe that if you were to ask any member of the management team what is one of the things you value most working at Butterball, they would mention our training program,” says Paulk. “This is our chance to give back to the management team and, in return, improve continually.”
Naturally, this never-stop-learning philosophy extends to plant associates as well. Mount Olive has several continuous learning programs to encourage associates. These include college tuition reimbursement, scholarships for employee children, supervisor apprentice programs, computer labs, roundtable sessions in each area of operation and daily performance reviews on key performance indicators (KPIs).
“The facility is aggressive in setting performance goals,” Paulk notes, adding that in some cases KPIs are reviewed hourly.
The training programs have paid off in multiple ways. First of all, Paulk says the plant has seen a “dramatic decline” in turnover rate in the last six months.
“Turnover is a common issue experienced within the industry and the facility had been faced with an increased turnover in 2008,” he explains. “As a result, we realized that we could not do business in the same way. We had to look at our practices and change them thus ensuring that we would have the associates to safely and efficiently run our processes.”
This year Butterball will continue to focus on worker safety and product quality. Paulk adds that planned 2009 capital expenditures will focus on automation and resource conservation.
“[Last year] Butterball leadership analyzed almost everything in our processes and worked to cut costs where possible - without sacrificing safety, food safety, customer service and the quality of our products,” he explains. “Butterball has always been committed to being a low-cost producer; however, 2008 took it to a new level of cost control and efficiency.”
To keep associates focused on efficiency and quality, Paulk says the Butterball Vision and Mission Statement are posted in every conference room throughout the facility.
“It reminds us of our responsibilities to our customers, associates and the community in which we live,” he says. “What truly differentiates us as a special facility is the people that we employ. It is the chemistry amongst our leadership and associates that have enabled us to continue to grow our customer base and lead our industry in product innovation.”
Just the Facts
Company:Butterball LLCFood plant(s) honored: Mount Olive, N.C.
Selection criteria: Worker Safety, Employee Programs
Employees: 2,600
Facility size: 650,000 square feet
Products: Cooked deli breasts, fresh tray pack turkey, ready-to-eat frozen breasts, turkey medallions, frozen raw turkey breasts, ready-to-cook frozen boneless turkey roasts, frozen whole turkeys.