BLOWMOLDER VISION INSPECTION SYSTEM
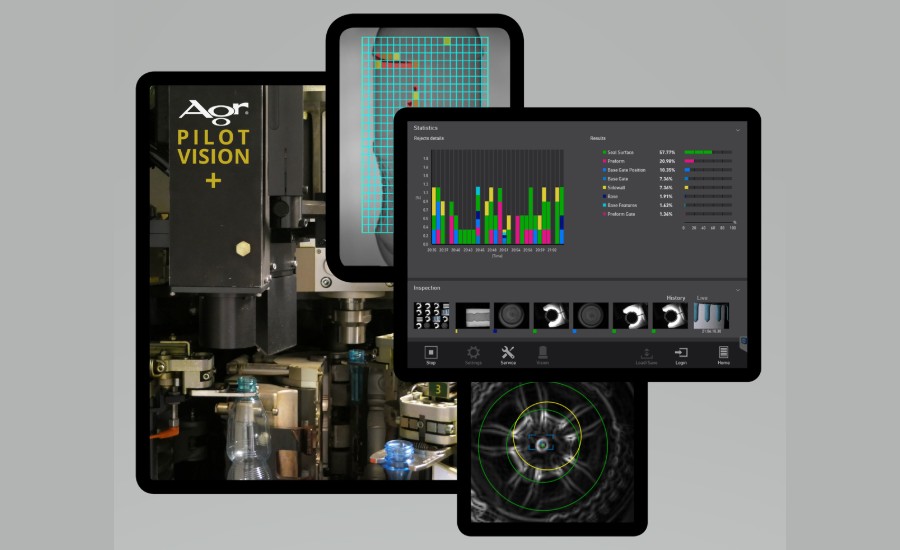
Agr International, Butler, Pa., presented the Pilot Vision+, an in-the-blowmolder vision system that is designed to work in conjunction with high-speed re-heat stretch blowmolding equipment. The Pilot Vision+ system offers a modular approach to defect detection that works within the blowmolder. The open architecture allows for simultaneous management of up to 6 cameras in multiple locations. Other features include color preform cameras for managing color variations, simple configuration and operation, large-screen user interface and defect categorization by mold/spindle and defect type. Pilot Vision+ can also be combined with Process Pilot for a total bottle management solution.
Jump to...
- Dynamic Conveyor Corp.
- Mettler-Toledo
- Inficon
- Septimatech Group, Inc.
- Beckhoff Automation LLC
- Triangle Package Machinery Co.
- Fortress Technology
- PMI Kyoto Packaging
- JLS Automation
- GEA North America
- Agr International Inc.
- Slideways Inc.
- OPTIMA Packaging Group
- NETSCH Pumps North America
- IMA Dairy & Food USA
- Signode Industrial Group
- Douglas Machine Inc.
- Peco InspX
- EDL Packaging Engineers Inc.
- Massman Automation Designs LLC
- PASE Group
- Meritech
- Morrison Container Handling Solutions
- Proseal UK Ltd.
- Regal Beloit Corp.
- RKW Group
- ID Technology
- Zip-Pak
- Coesia Group
- Rockwell Automation
- Sonoco Products Co.
- Wexar Bel
- Thermo Fisher Scientific Product Inspection
- tna
- SICK Inc.
- ORBIS Corp.
- Charter NEX
- BW Packaging Systems
- Quest Industrial
- Ossid
- Lantech
- NORD Gear Corp.
- Texwrap Packaging Systems
- Datalogic ADC Inc.
- Synerlink
- Think Plastic Brazil
- Epson America
- Mondi North America
- Toshiba America
- Unibloc-Pump, Inc.
- Silgan Dispensing Systems
- Silgan Equipment
- Eriez
- PPI Technologies Group
Agr also featured the Process Pilot system with advanced thin-wall capability. Introduced earlier this year, this tool is ideally suited for facilitating the production of ultralight bottles. The Process Pilot system works in conjunction with the blowmolder to continuously measure material distribution on every bottle, and proactively manage the blowmolder to maintain optimal material distribution.
Agr International Inc.
724-482-2163
www.agrintl.com
LEVELERS FOR CONVEYORS & PACKAGING EQUIPMENT
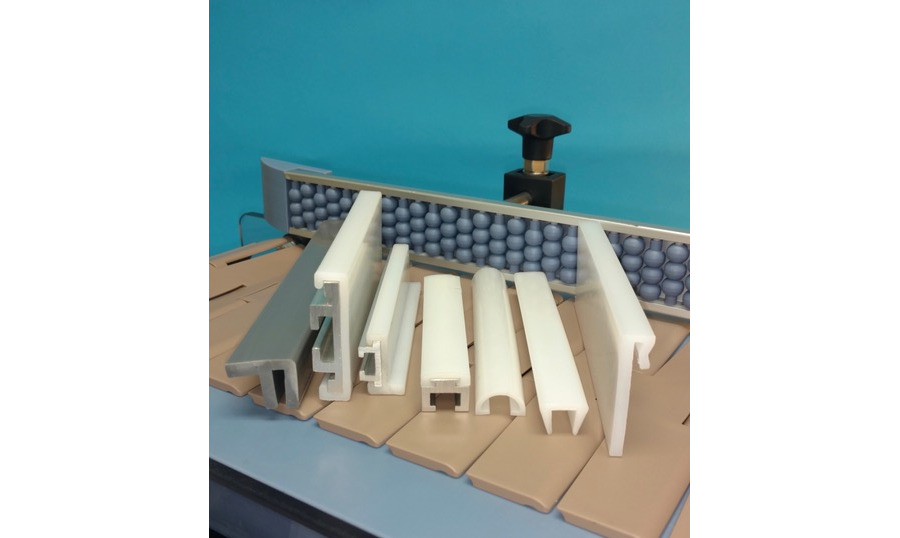
SLIDEWAYS, Worcester, Mass., featured its full range of standard components and levelers for conveyors and packaging equipment, including wear components, guide rails, SlideTrax for side flexing and straight running chain, roller chain guides and sprockets, UHMW profiles, rollers, pulleys, bushings and bearings for harsh environments.
For custom component users, SLIDEWAYS shows an extensive range of unique and proven solutions for mechanical wear, conveying and packaging applications.
Slideways Inc.
800-298-7543
www.slideways.com
FLEXIBLE PACKAGING SOLUTIONS FOR FOOD, BEVERAGE APPLICATIONS
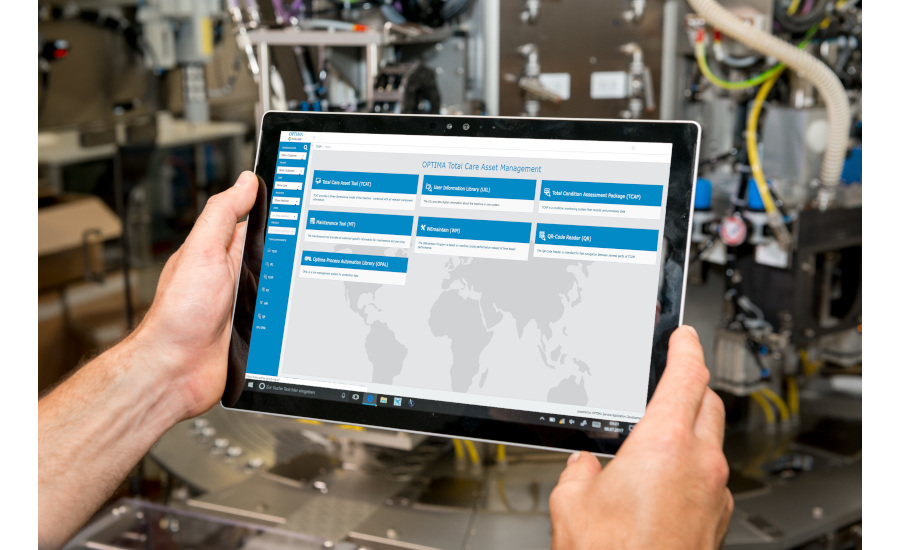
Optima Packaging Group, Germany, presented highly flexible packaging solutions for food and beverages products.
Optima offers a wide range of filling and dosing methods. For example, paste-like and powdered foods are processed in portion packs similar to coffee packaging. Optima also uses robotics, film, foil and plastic processing, as well as “cobots” and converting functions to produce a range of flexible machines from entry-level to fully automated, highly efficient lines.
Optima opened a new logistics center in Schwaebisch Hall, Germany, using comprehensive scientific process engineering (CSPE) to reduce time-to-market and optimize processes.
Optima's Total Care concept includes Smart Services, which include complex simulations during the project-planning phase, as well as the use of virtual reality technologies for supporting maintenance and repairs. The OPAL line management system enables Optima to offer an additional component for highly efficient, long-term processes. The cross-manufacturer 4.0 industry application comprehensively generates and analyzes production data to systematically unlock productivity potential.
OPTIMA packaging group GmbH
+49 (0)791 / 506-1472
www.optima-packaging.com
SANITARY PUMPS
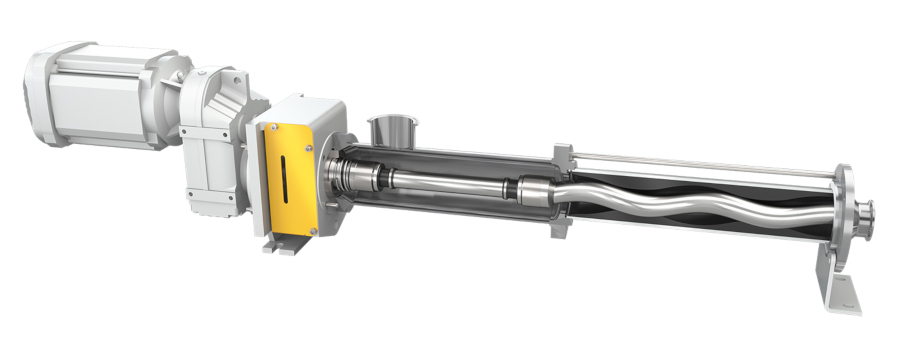
NETZSCH Pumps North America, LLC, Exton, Pa., highlighted its sanitary pumps ideal for a wide range of food applications.
The revolutionary T.SANO rotary lobe pump, for instance, features the FSIP (full-service-in-place) design.
The TORNADO T.SANO boasts a smooth, flat profile rotor that features several options specifically developed to meet the process industry requirements. Self-priming and valve-less, the TORNADO T.SANO is ideal for any kind of liquid, including media-containing gas, solids or fibrous matter, and can be used in intermittent, continuous or metering applications.
The NEMO BY Sanitary Prime pump is an FDA-compliant solution for sensitive, abrasive and high viscosity pumping needs. From low viscosity media to products barely capable of flowing, with or without solid content, shear-sensitive, sticky or abrasive, the NEMO BY Sanitary Prime pump conveys even difficult substance gently and with low pulsation. It is a good choice for high acids, high sugars and low water content, as well as pet foods and raw materials before being processed.
Also on display was the NEMO BH Sanitary Advanced pump, which are ideal for meats, dairy products and sauces, and for any products requiring gentle handling and/or high viscosity. They are appropriate for clean-in-place (CIP) processes, and meet 3A standard requirements.
The NEMO BH Sanitary Advanced Plus pump meets the strictest hygienic standards, and can be used to minimize CIP time. This pump is a good choice for high-risk products, and is ideal for liquid eggs, white mass, cultures and low acid pasteurized or protein products.
The NEMO BO Sanitary Prime Open Hopper pump is an FDA-compliant pump for non-free-flowing applications. Designed with an integrated auger that forces non-flowing product into the pumping area, the NEMO BO Sanitary Prime Hopper pump is ideal for raw material handling, fruits, vegetables, meat emulsions and sticky products.
NETZSCH Pumps North America, LLC
610-363-8010
https://pumps.netzsch.com
MULTI-LANE FORM-FILL-SEAL MACHINES
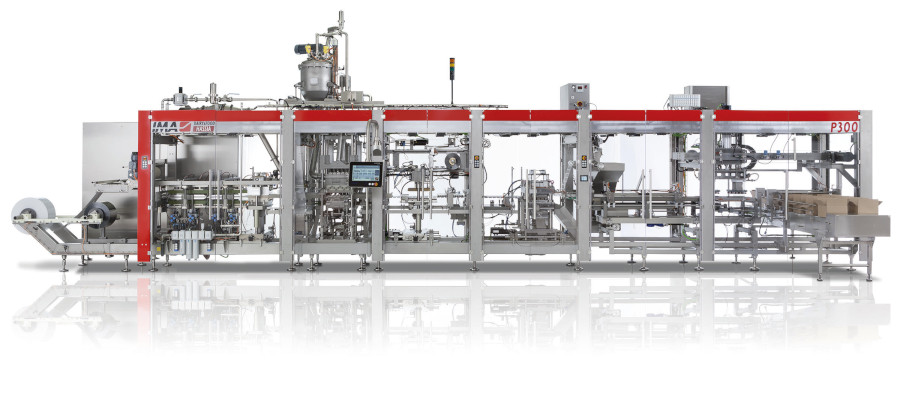
IMA Dairy & Food, Leominster, Mass., introduced new and enhanced packaging machines.
Hassia’s form-fill-seal (FFS) M-Flex Series F600 Sachet Machine produces 4-sided sealed sachets at speeds up to 80 cycles per minute and on as many as 16 lanes. The F600 also offers single-roll functionality, an improvement over 2-roll formats, and the units run a single wide roll located at floor level for easy changeover and front-and-back sachet registration. The F600 can handle rolls as wide as 1,200 mm with a diameter of 800 mm, which can yield up to 16 hours of run time between roll changes. The F600’s careful product handling makes it suitable for clean-in-place and steam-in-place dosing units. The machine’s control concepts are highly versatile, and include opportunities for integration with customer-specific systems. The unit can handle all common packaging materials suitable for heat-sealing.
Hassia also showcased the other member of the M-Flex Series—the S600 Stick Pack Machine—a multi-lane FFS module for the production of 3-sided stick packages. With a typical processing speed of up to 42,200 stick packs per hour, the S600 complies with customer/product-specific requirements.
Hassia also showcased the P500 Portion Pack Machine, part of its P-Series line of FFS portion pack equipment. Capable of handling web up to 590mm wide at forming depths up to 40mm, the high-performance P500 is suitable for a broad variety of cup designs and materials. A key benefit of the P500 is its use of comparably less packaging material. This is due to a combination of attributes, including its use of forming material of minimal thickness to avoid over-packaging; minimal punch waste from the low-waste punch unit; and volume-saving overlapping packing configuration for boxes and trays. Depending on the specific product, the P500 can achieve speeds up to 108,000 cups per hour.
The P-Series of portion pack machines also includes the P300, which features a new frame and guarding package for easier machine accessibility. Both the P300 and P500 offer hygiene levels up to FDA-filed, low-acid aseptic, and incorporate a new “cell board conveyor” discharge that controls round cups through case packing.
Erca showcased the EFS, a new format flexible indexing platform for pre-formed cups. Modular in design with stainless-steel construction and servo-operations, it allows for flexibility with filling stations, pre-fill and post-fill for wet or dry ingredients. The chainless solution for cup transportation enables format flexibility and precision index positioning throughout the machine. Capable of filling cups up to a diameter of 130mm, the EFS filling and sealing machine is suitable for a broad variety of products such as yogurt, fresh cheese, white cheese (curd), cottage cheese, single and multi-layer desserts, aerated mousse products, deli salads, dips, dressings, hot-filled sauces, soups, jams, fruit purees, pet food and more. Key benefits of the EFS are the format flexibility (quick release, tool free), the chainless drive (no chain stretch, no regular adjustment, less cup cassettes), the modular design and construction, the recipe functionality, the multi-fill possibilities (over track or remote fillers) and its improved hygiene options (UVC, Pulse light, H2O2). The machine will be available in hygiene levels clean or ultra-clean.
IMA Dairy & Food USA, Inc.
978-549-4823
https://imadairyfood.com
CORPORATE BRAND REFRESH, E-COMMERCE TECHNOLOGIES
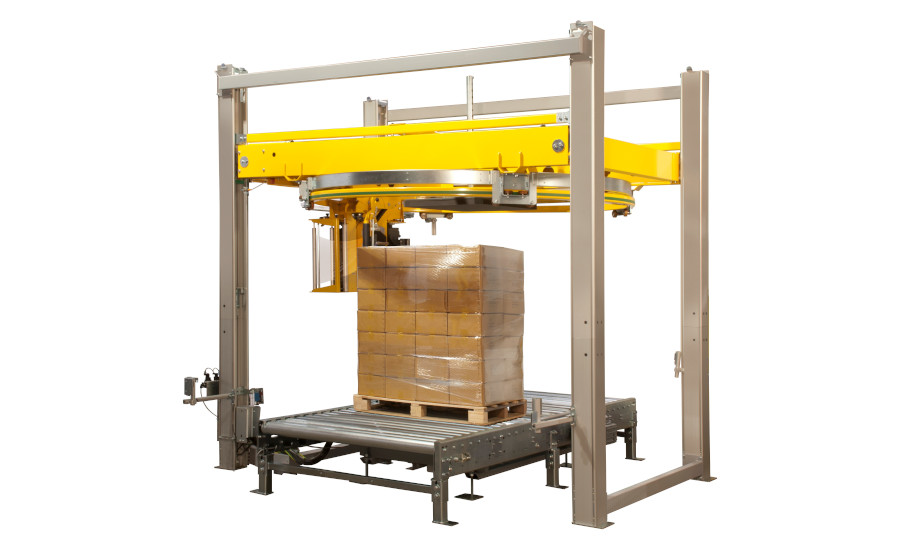
Signode Industrial Group, Glenview, Ill., introduced its new brand, which consists of a more streamlined business model and groups several products under key application categories such as pack, bundle, unitize, warehouse and transport. Signode plans to further unify offerings under a new company brand identity to showcase integrated solutions fit for the global marketplace.
In addition, Signode highlighted two of its e-commerce technology pairings.
The first transit packaging combination comprises the H. BÖHL orbital stretch wrapper from SPG Packaging Systems GmbH, Germany, and Little David Case Sealer SP-304 from Loveshaw, South Canaan, Pa. The orbital wrapper secures products to trays, while the case sealer enables proper closure and sealing of the protective box. The H. BÖHL orbital stretch wrapper eliminates loose fill packaging material by providing superior load stability. The product is first placed on a suitable tray, with material type, size and weight determined by product, and placed inside the wrapper. The unique orbital design wraps the stretch film over and under the product, tightly securing it to the tray. After the product is placed in the outer box, it is safely secured, minimizing, or in some cases, eliminating additional product protection or dunnage. Engineered for a range of uniform cases and industrial environments, the Little David Case Sealer SP-304 features an automated three-flap folder with universal bottom flap folding bars for fast and uniform closure while automated taping seals the box. Equipped with interchangeable tape cartridges and top squeezer rollers, the Little David Case Sealer SP-304 features an automated CaseLocker ST tape cartridge that requires no lubrication and helps avoid the twisting motions known to cause carpal tunnel syndrome. The tape cartridge’s knife guard system means that workers are not exposed to the blade.
The second transit-packaging pairing features the Octopus Compact 20 automatic rotary ring stretch wrapper from Muller LCS, Glenview, Ill., working in concert with StorFast, Signode’s cart-based, high-density automated storage and retrieval system. Octopus Compact 20 automatic rotary ring stretch wrapper is versatile for a variety of applications and environments. Compact and intuitive, the technology is engineered for manufacturers looking to increase productivity without compromising space or budgets. The modular design of the machine further allows for customized options to solve a host of pallet unitizing challenges.
Signode Industrial Group
800-323-2464
www.signodegroup.com
CASE PACKERS
Douglas Machine, Inc., Alexandria, Minn., showcased four of its cutting-edge machines.
CpONE Intermittent Motion Case Packer consists of 40% fewer parts and 40% fewer change points.
TriVex SL Case Packer is a versatile and innovative retail-ready case packer for pouches and bags.
Spectrum Multipacker is a beverage cartoner and variety pack solution that maximizes output and minimizes labor.
And, Contour M‐60 Multiwrapper enables new robotic product registration and metering system for efficiency, accessibility and flexibility. It also produces film-only shrink bundles in single or multiple lanes for increased throughput.
Douglas Machine Inc.
320-763-6587
www.douglas-machine.com
HIGH-RESOLUTION IMAGING TECHNOLOGY
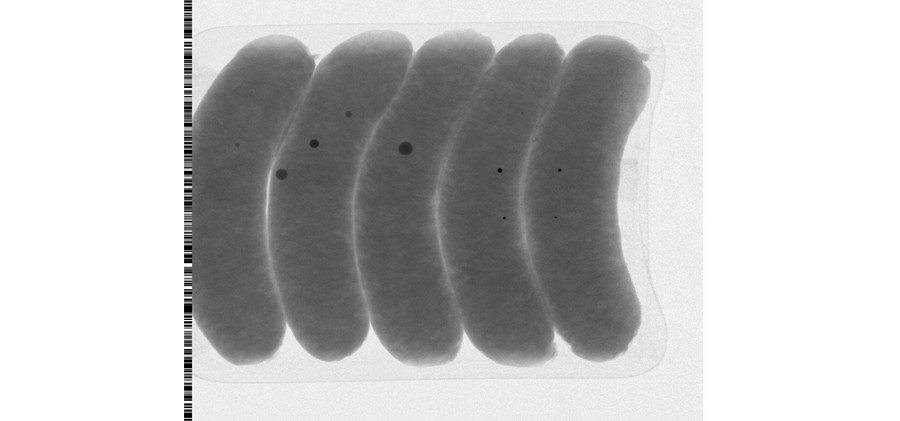
Peco-InspX, San Carlos, Calif., announced HDRX imaging technology, which captures extremely high-resolution images of products to detect foreign material and minimize false rejects.
HDRX also delivers high image resolution at normal production line speeds within power settings used by traditional x-ray systems used in food and beverage applications.
This automated x-ray inspection technology is available across the Peco-InspX x-ray system product line, including side-view, top-down and dual energy systems.
Peco InspX
877-722-6875
www.pecoinspx.com
SINGLE ROLL WRAPPER PACKAGES TRAYED, TRAYLESS PRODUCTS
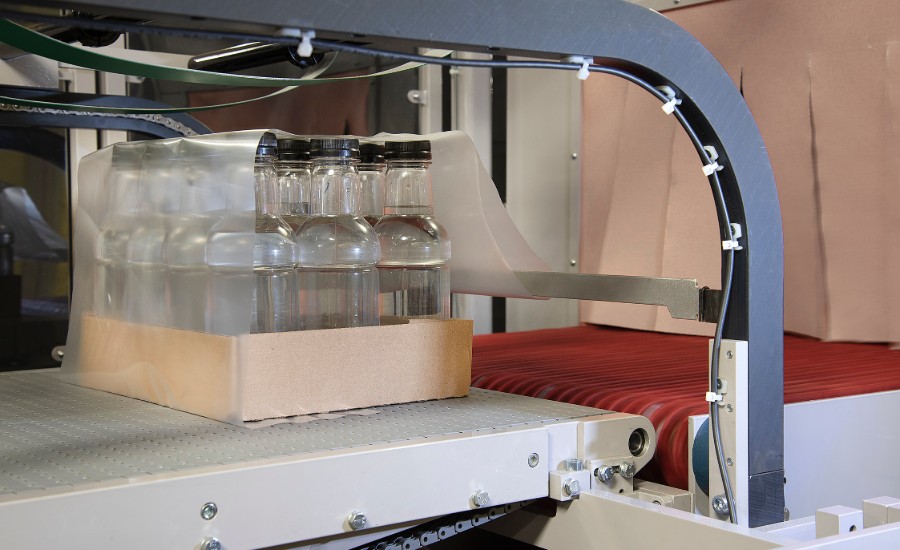
The new EDL Model 22-45 single roll product wrapping system from EDL Packaging, a Massman Co., Green Bay, Wis., wraps both trayed and trayless products at rates up to 45 packages per minute. This includes trayed packaged food products, pet foods, dairy products, mixed multipacks and other packaged products, as well as untrayed single products and multipacks of containers.
This new system delivers reliable, repeatable wrapping performance at medium speeds in a real-time production environment, with the ability to accurately control print registration. A welded tubular frame controls vibration to ensure consistent wrapping output and production throughput.
The servo-driven inline system can be easily integrated into an existing production line, and is designed to handle products up to 16 inches in length, 12 inches high and 20 inches wide. The system wraps using 1.5- to 3-mil film in segments up to 55 inches long and 22 inches wide. The SRW 22-45 can wrap products using either clear plastic film, random printed or print-registered film. Trayed products can be wrapped in corrugated trays or on flat pads. During the servo-driven wrapping process, products do not stop, but are in continuous motion as film is applied and cut, maximizing productivity. A high-efficiency shrink tunnel completes the wrap sealing process.
The SRW 22-45 system’s welded tubular steel frame has a powder-coated surface finish. Legs are threaded to be adjustable up to 2 inches for system leveling. Additional options include a film loading cart and an inline cradle splicer for speedy film changeovers.
EDL Packaging Engineers, Inc., a Massman Co.
920-336-7744
www.edlpackaging.com
TOP-ONLY CASE SEALER
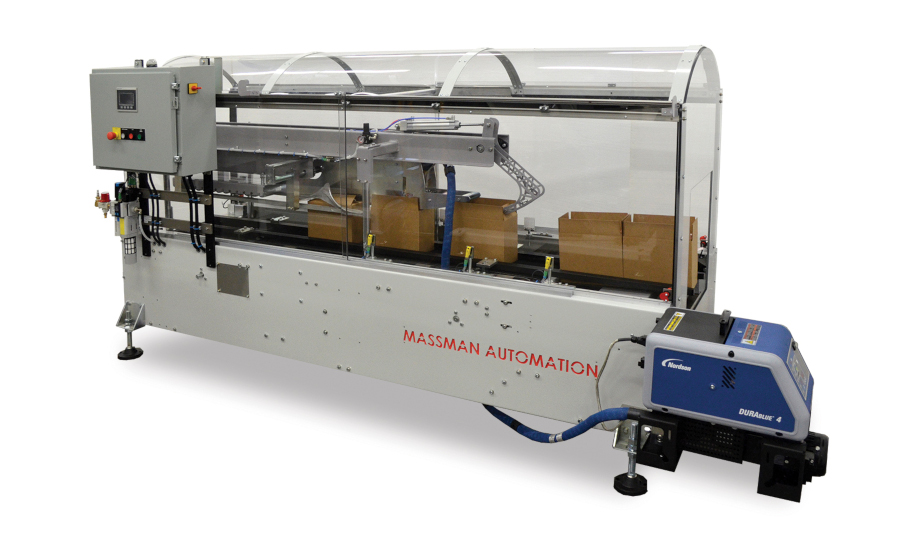
Massman Automation Designs, LLC, Vilard, Minn., introduced a new compact HMT-Mini top-only case sealer.
This new sealer incorporates an innovative modular construction that allows specific features of the sealer to be changed out to facilitate future sealer design changes.
The standard HMT-Mini top-seals cases using either glue or tape at speeds of up to 1,500 cases per hour. An optional, more advanced sealer incorporating extended compression seals at rates of up to 3,000 cases per hour. The fully-automatic sealer features robust, heavy-duty construction, speedy changeover to new case sizes and is completely enclosed. The system’s transparent enclosure offers increased visibility of the operation, and interlocked Lexan access doors on either side of the enclosure give greater access to the machinery without sacrificing safety.
The HMT-Mini seals standard cases up to 18 inches long, 16 inches wide and 16 inches deep.
Massman Automation Designs, LLC
320-554-3611
www.massmanllc.com
SEMI-AUTOMATIC DRUM, TOTE FILLING MACHINE
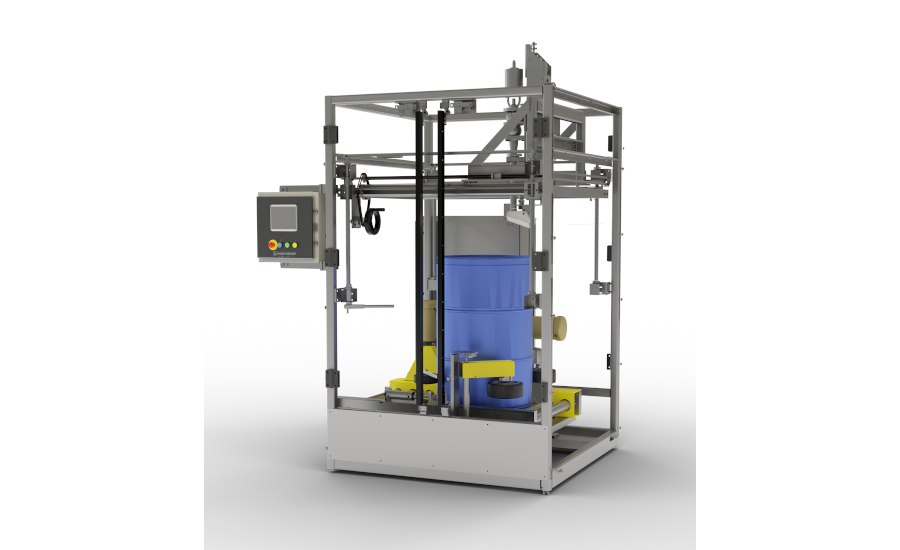
PASE Group Massman, LLC, a Massman Co., Eagan, Minn., announced its Dual Lance Semi-Automatic Drum and Tote Filling Machine, which provides high accuracy semi-automatic net weight filling while allowing for two different products to be filled by the same filling machine. Two precision-made proportional fill lances mounted on separate ball screw drives deliver independent top, inside or bottom filling of drums or totes. This filling machine controls two separate product pumps as needed, as each fill lance operates under its own PLC-based filling recipe. Benefits include fast product changeovers, no product cross-contamination and the ability to fill different size drums with two products on the same pallet, eliminating the need to re-palletize drums later. Machine features include top fill, inside fill or bottom fill operation; HMI mounted on operator-controlled handlebar; 3A-rated stainless-steel fill lances; Allen Bradley PLC for machine control; filling recipe management and machine diagnostics; drip cups and pump controls. Options include explosion-proof controls package, flush stations, pump carts and a wide variety of gravity and smart-powered conveyor packages.
PASE Group also introduced its Automatic Single Drum Filling Machine, which provides net weight filling with automatic bung detection and orientation. This enables the compact filling machine to accept single drums without the need to orientate the bung location by hand. Empty drums feed into the filling machine via a powered conveyor and rotate by an innovative motorized dual-wheel drive system that allows a small overhead laser-based vision system to quickly find the bung location. Once the bung is located, the dual-wheel drive mechanism releases the drum, and is quickly tared and automatically net-weight-filled according to the stored filling recipe for that product. Filled drums are then palletized and shrink-wrapped for shipping. The machine performs top fill and inside fill, or bottom filling of drums for foamy applications. Available options include custom in-feed and out-feed conveyance, fume hoods, labelers, sanitary design and explosion-proof packages, as well as a variety of drip cups and fume handling options. The system also features a large color touchscreen HMI for machine operation, recipe management and real-time monitoring of the filling process.
PASE Group
608-316-6324
www.pasegroup.com