SUSTAINABLE PACKAGING INITIATIVE
Sonoco, Hartsville, S.C., created the EnviroSense sustainable packaging initiative that includes a range of packaging materials, including cans made from 100% recycled paperboard, rigid plastic packaging containing post-consumer recycled content, mono-material flexible pouches that are recyclable and innovative packaging made from agricultural fibers.
Jump to...
- Dynamic Conveyor Corp.
- Mettler-Toledo
- Inficon
- Septimatech Group, Inc.
- Beckhoff Automation LLC
- Triangle Package Machinery Co.
- Fortress Technology
- PMI Kyoto Packaging
- JLS Automation
- GEA North America
- Agr International Inc.
- Slideways Inc.
- OPTIMA Packaging Group
- NETSCH Pumps North America
- IMA Dairy & Food USA
- Signode Industrial Group
- Douglas Machine Inc.
- Peco InspX
- EDL Packaging Engineers Inc.
- Massman Automation Designs LLC
- PASE Group
- Meritech
- Morrison Container Handling Solutions
- Proseal UK Ltd.
- Regal Beloit Corp.
- RKW Group
- ID Technology
- Zip-Pak
- Coesia Group
- Rockwell Automation
- Sonoco Products Co.
- Wexar Bel
- Thermo Fisher Scientific Product Inspection
- tna
- SICK Inc.
- ORBIS Corp.
- Charter NEX
- BW Packaging Systems
- Quest Industrial
- Ossid
- Lantech
- NORD Gear Corp.
- Texwrap Packaging Systems
- Datalogic ADC Inc.
- Synerlink
- Think Plastic Brazil
- Epson America
- Mondi North America
- Toshiba America
- Unibloc-Pump, Inc.
- Silgan Dispensing Systems
- Silgan Equipment
- Eriez
- PPI Technologies Group
EnviroSense products are designed to incorporate a number of elements associated with more sustainable packaging such as reduced environmental impact, optimized package-to-product ratio and shipping optimization, increased use of recycled content, recyclability, fiber sourcing, compostability and the use of bio-based materials.
Sonoco Products Co.
843-383-7000
www.sonoco.com
CONVEYOR, SEALER, CASE FORMER, WORK CELL IN ONE
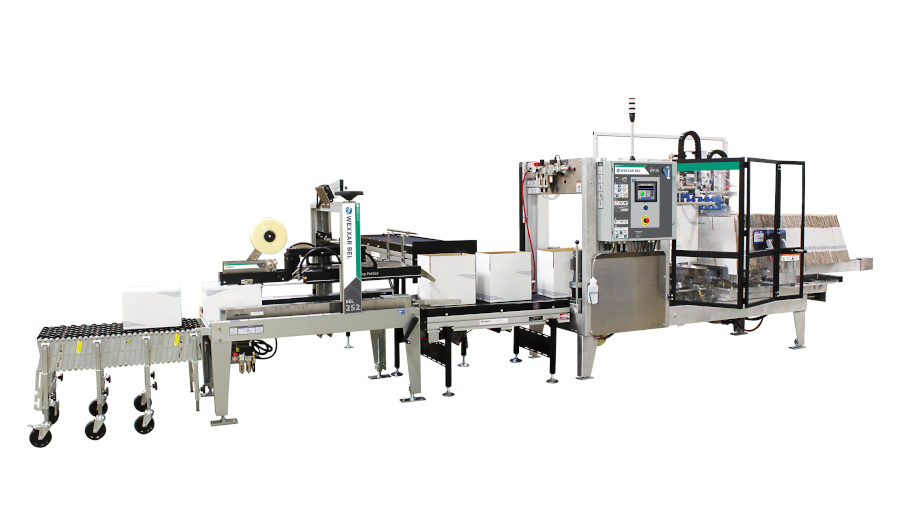
Wexxar Bel, Canada, debuted the new Flex E Pack system, a modular engineering solution that provides end users with the flexibility to integrate the right case former, product delivery conveyor, work cell and sealer that best meets their applications.
Meanwhile, the 2-person work cell best utilizes Pack Control to hand pack product into cases as efficiently as possible. With Pack Control, work cells can be individually activated, depending on the availability of operators. Pack Control provides each cell the ability to adjust their line with minimal impact to overall production rates.
The Flex E Pack system includes the Wexxar WF20 fully automatic case former/case erector, which produces up to 20 cases per minute and is available in tape or hot melt glue sealing. The Flex E Pack system can be paired with any Wexxar case former, depending on application needs.
Case sealing is handled by the BEL 252 Fully Automatic Top & Bottom Tape Case Sealer, and features the Uni-Drive System, which powers both side belts from a single motor, keeping them synchronized to provide a square seal even after prolonged use. Additionally, the line includes a PD50 bi-directional conveyor, which enables products to flow in opposite directions from the same conveyor platform.
The Flex E Pack is ideal for packaging lines with variable product flow and packing situations due to frequent case size changes, different case sizes and pack configurations, limited floor space, manual inspection of products, limited technical staff, high price of automated case packers and erectors and high SKU volume.
Features and benefits of the Flex E Pack system include:
- All-in-one, integrated case forming, packing and sealing system.
- Up to 20 cases per minute.
- 1- or 2-person packing station.
- Ergonomic industrial foot switch.
- Snap Folder safe flap folding technology.
- User-friendly touchscreen controls.
- Illustrated, color-coded adjustment instructions.
Wexxar Bel
888-565-3219
www.wexxar.com
INSPECTION, DETECTION, CHECKWEIGHING TECHNOLOGY
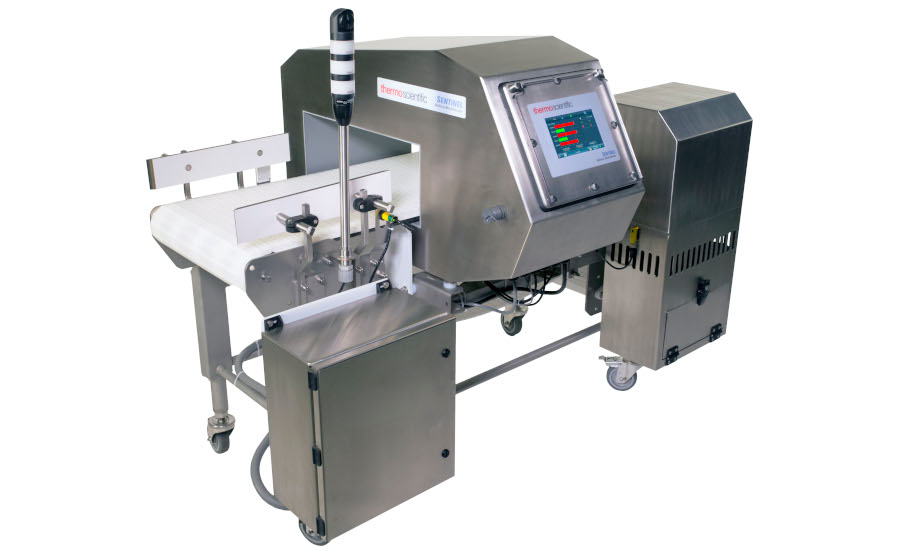
Thermo Fisher Scientific, Minneapolis, displayed a wide array of inspection, detection and checkweighing technology.
For starters, the Thermo Scientific Sentinel 3000 multiscan metal detector is the smallest model in the line of Sentinel metal detectors, and mounts on the frame of Thermo Scientific VersaWeigh and Versa GP checkweighers. The Sentinel 3000 detector is said to be the first multi-frequency metal detector specifically designed for metal detection-checkweighing combination systems in food production. Integrating the detector onto the checkweigher frame eliminates the need for an external metal detector conveyor. New harmonized Versa checkweigher software incorporates capability to operate the checkweigher and metal detector from one screen, and is designed to improve usability and reduce training time. The Sentinel 3000 metal detector features multiscan technology, which allows users to select up to five frequencies from 50-1,000 kHz and scan through each frequency at a rapid rate. It effectively acts like five metal detectors in one. The technology also is devised to increase the probability that all random sizes, shapes and types of metal foreign objects are found before food products reach consumers. The Sentinel 3000 metal detector is designed for a wide range of food applications, including dairy, meat, poultry, fruit, vegetables and bread.
For more information on the Thermo Scientific Sentinel 3000 multiscan
The NextGuard X-ray Detection System is an easy-to-use, entry-level x-ray inspection system that offers advanced capabilities for finding metallic and non-metallic foreign objects. It uses a non-linear detector designed to improve detection of dense objects.
The Versa Flex Checkweigher with APEX 300 Metal Detector provides accurate weight control for dry applications, and helps assure that product is free of metal contaminants.
The Xpert B600 X-ray Inspection System is designed specifically for x-ray inspection of high-value bulk food products, such as seeds, nuts, fruits and vegetables, prior to further processing.
The Versa 8120 chain checkweigher provides high-speed weighing, control and reject functions for cartons, cans, bottles and rigid packages, and features a rugged chain design for easy cleaning and maintenance.
Thermo Fisher Scientific Product Inspection
763-783-2500
www.thermoscientific.com/productinspection
SINGLE-SOURCE SOLUTIONS CAPABILITIES
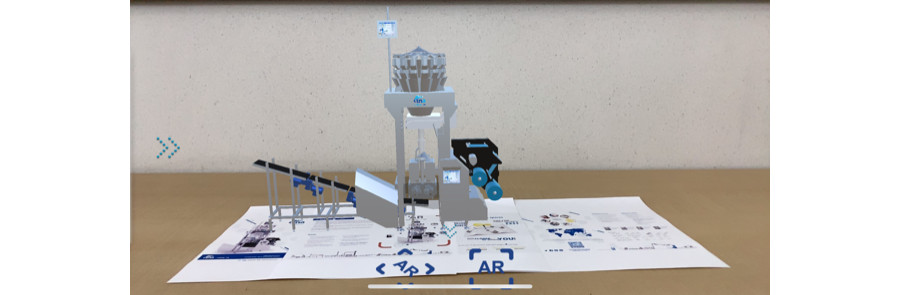
tna, Dallas, Texas, demonstrated its capabilities to deliver single-source solutions and boost throughput capacity and speed at scale without increasing waste or compromising on quality and accuracy.
This immersive, interactive experience in a multi-sensory environment enabled visitors to explore tna’s comprehensive capabilities as a single-source solutions provider.
tna leveraged augmented reality technologies on everything from high-performance batch fryers to distribution and packaging lines.
tna
972-462-6500
www.tnasolutions.com
SOLUTIONS FOR ERROR-PROOF PACKAGING & IMPLEMENTING INDUSTRY 4.0
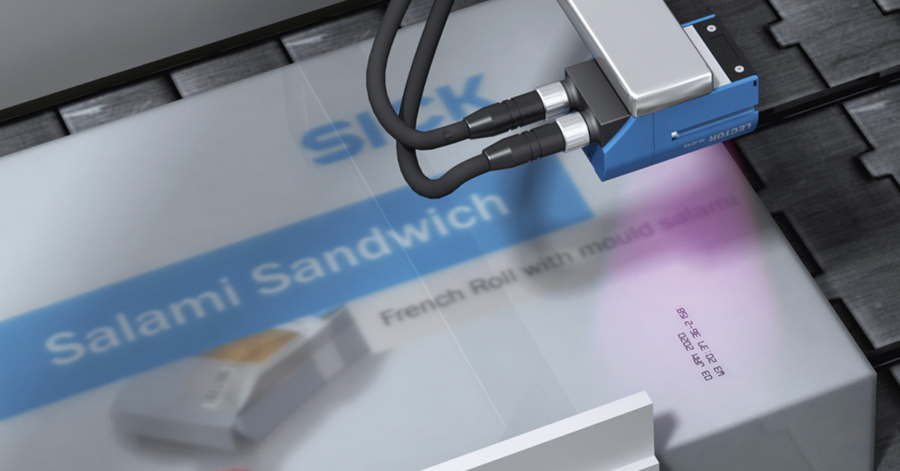
SICK, Inc., Minneapolis, partnered with AutoCoding Systems, Inc., London, to develop complete sensor and software solutions for error-proof packaging. This full coding management and packaging verification solution provides insurance against any potential coding and packaging errors.
Benefits include:
- Controlled deployment and set-up of date coding equipment.
- Central configuration matches product specifications with device profiles.
- In-line barcode scanning of 1D and/or 2D barcodes with Lector image-based code readers.
- Validation of all packaging-related attributes like barcode verification and placement.
- Achieve end-to-end control of the packaging process, even with existing equipment.
- Costs based on a simple licensing model according to the number of devices on the line.
- Remote access to all lines via PC, industrial HMI, tablet or smartphone.
- Multiple devices across many lines can be controlled from one central point.
Starting with device management, including set-up and control of the equipment, SICK helps to implement this solution on packaging lines to provide effective coding management and verification. This includes paperless quality and vision inspection. Once installed, the machine provides packaging and label verification. Full audit records are also available for traceability purposes. AutoCoding’s software effectively manages the deployment of coding data and the checking of packaging before products leave the factory. SICK sensors verify the correct code was used and printed, helping to validate codes and prevent recalls. SICK products and AutoCoding’s coding and packaging verification solutions can be used in a range of applications. SICK’s Lector image-based code readers are used for 1D and 2D barcode scanning to check retail barcodes, backweb label barcodes and packaging artwork barcodes. AutoCoding also has a number of vision installations that incorporate SICK’s ICR image-based code readers, IVC-3D cameras and the InspectorP series of cameras. In addition, AutoCoding’s advanced coding management software is designed to control and manage a wide range of different packaging line devices. The full solution provides dynamic control of the packaging line, ensuring that it stops in the event of too many misreads or no-reads detected from the SICK sensor or if a device malfunction is detected. SICK’s solution also enables manufacturers to use a single system to control multiple devices from different vendors. The devices may perform different functions, such as coding, inspection, labeling and verification, but all exist on the same line. This complete solution provides the consumer goods industry a method to greatly reduce date-coding errors and downtime related to product changeovers.
SICK also demonstrated its 4.0 NOW Factory sensor technology and dashboard, which makes it easier to implement improvements and new innovations. Sensor intelligence entails programmable and self-learning cameras, reliable safety sensors for human-robot collaboration and complete solutions for navigating autonomous guided vehicles. All of these devices connect with one another via the cloud, implementing Industry 4.0 along the entire value-creation process. Sensors and other technology can then be accessed via the 4.0 NOW Cockpit, a dashboard that simulates sensors and provides a live view of the sensors at work. Decentralized intelligence in the sensors (edge computing) forms the basis for flexible control of production processes in the smart factory. Additional cloud intelligence in the form of data analyses and applications allow the use of self-learning mechanisms in the sensors, increasing their adaptability to production-related changes. Some sensors transmit data directly to a level where information is needed. And, for more complex scenarios, data collection devices can harvest data from multiple sensors. The data is then aggregated, filtered and prepared to be transmitted to the level where information can be visualized. This data includes product-related information (status of a batch process or count of product) or vision inspection information that provides quality-related data. 4.0 NOW Factory is applicable for production logistics, flexible production, track-and-trace technology, safety and quality control.
SICK opened a 4.0 NOW factory in Freiburg, Germany, in February. It consists of 12 independent technology modules designed to efficiently produce seven SICK product families with over 600,000 variants. With the 4.0 NOW Cockpit, manufacturers gain connectivity to sensors via the TDC-E Gateway that then enables them to interact with the installed applications and transfer data to the dashboard. The supply chain is taken over by driverless transport systems together with collision prevention solutions. The data from all the sensors in the smart factory are evaluated on a large display, giving visitors a constant overview of logistical and production processes as well as key performance indicators.
SICK is also said to be the first manufacturer to offer a comprehensive range of solutions along the entire value creation change from a single source. Indoor localization makes it possible to manage complex networks, create transparency and ensure speedy production. Assets in a factory are tracked continuously using localization solutions—known as indoor GPS—and their space-time coordinates can be continuously recorded and stored. Having this data means complete transparency about all the important movements on the shop floor. All the established technologies—ultra wide-band tags, LiDAR Contour Mapping, line guidance sensors and infrastructure sensors—record either their own position or the position of the desired objects. Depending on the application as well as the positioning accuracy and update rate required, the right technology is selected or various technologies are combined with each other. Localization technology is one of the key factors in achieving Industry 4.0, as it can be used to boost optimization potential in several areas by allowing for agile planning of production and logistics processes. Localization data gives companies a high level of transparency and understanding of all production-related assets, load carriers and loading equipment. As a result, travel paths are optimized and adapted dynamically. Set-up times can be prepared or scheduled flexibly. The material flow can be planned and controlled based on consumption.
Meanwhile, the TriSpector1000 is a vision sensor that provides 3D inspection for flexible automation. The TriSpector1000 is a stand-alone, configurable 3D vision sensor that inspects objects regardless of variations in object color, height, shape or position. In addition, intensity data enhances 3D navigation and allows the sensor to check for object rotation or the presence of a label or printed pattern. Useful in 3D robot guidance, profile monitoring, assembly checks and quality inspections, the TriSpector1000 can be tailor-made to fit any application thanks to SICK’s AppSpace development framework. The TriSpector1000 is especially suited for solving quality control applications in the consumer goods and packaging industry, and can be used for volume and thickness measurement and inspection of box integrity, including content verification, completeness and emptiness checks. Within these industries, common quality issues can be easily resolved with automated quality checks using vision-sensor technology, including missing caps, lids or open containers; misapplied labels; and incorrect labels. The TriSpector1000 also boasts easy configuration, commissioning and operation thanks to an intuitive user interface and embedded image analysis. Factory calibrated data also simplifies setup and reduces time and effort.
SICK Inc.
952-941-6780
www.sickusa.com
RETAIL SUPPLY CHAIN SOLUTIONS
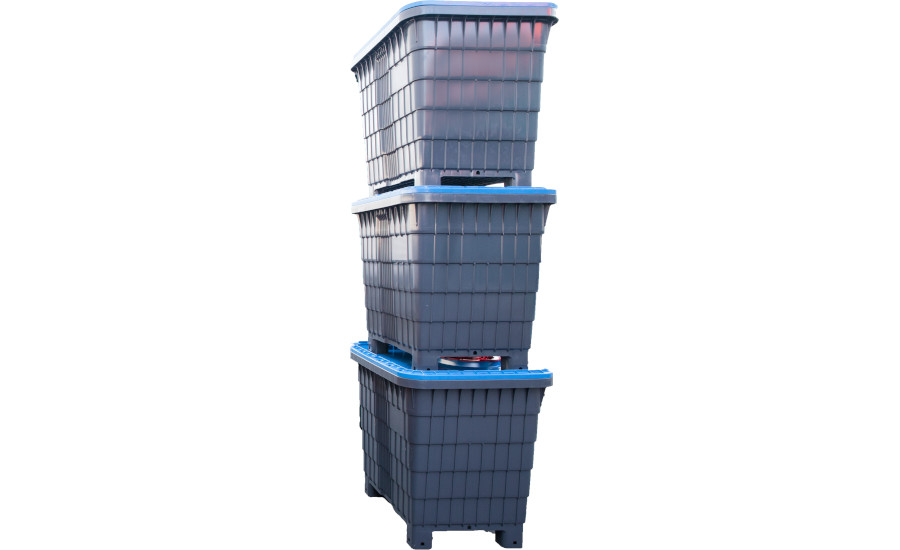
ORBIS Corp., Oconomowoc, Wis., highlighted several of its retail supply chain solutions.
For example, MultiTank for bulk handling,
- Efficient alternative to 55-gallon drums, intermediate bulk container tanks for wet and dry ingredients.
- Offers 6:1 return ratio and saves up to 75% in storage space.
- Innovative airtight and watertight lid design.
XpressBulk milk delivery system
- Fully reusable, retail-ready, 1-touch merchandising system designed for retail deliveries.
- Allows for easy transport off the truck and right into the retail environment for quicker unload.
- No unpacking or additional touches needed, as consumers shop directly from XpressBulk.
HDMX4048-46 MaxCube series,
- Collapsible straight-wall container, offered in the industry standard 40x48-inch footprint, and holds up to 1,200 pounds and more than 40 cubic feet of product.
- Improved sidewall performance for a long service life.
- Foot cap wear plates for long performance in rugged environments.
Intelligent packaging (enabling tracking and management of reusable assets),
- Improves visibility throughout the supply chain.
- Reduces theft, breakage and loss.
- Reduces dwell time.
40-by-48-inch pallets with Proliant,
- Fire-retardant plastic material for use in select plastic pallets, including rackable and stackable styles, in footprints from 36x40 inches to 48x48 inches.
- Halogen- and bromine-free material that is fully recyclable.
- FM approvals-certified and FDA-compliant.
E-commerce totes,
- Family of all-plastic totes designed to work in many picking environments — manual and highly automated.
- Dimensionally consistent for seamless integration with today’s high-speed systems.
- Made in a variety of footprints and often customized to meet system requirements.
ORBIS also launched several items for the industrial setting, including its BulkPak HDMP 4845 series, thermoformed dunnage and AdjustaPak, an adjustable sliding dunnage system.
ORBIS Corp.
800-890-7292
www.orbiscorporation.com
HIGH-CLARITY PRINT FILM
Charter NEX, Milton, Wis., introduced new GreenArrow High Clarity PE Print Film solution.
This film was designed to mimic the properties of PET or OPP, but in an all-polyethylene format to produce store drop-off recyclable packaging for the How2Recycle program.
Also new is Charter NEX’s new high-barrier, metallized PE sealant film designed and developed in conjunction with Celplast Metallized Products, Canada. This new fully developed all-PE recyclable pet food package uses high contents of post-consumer recycled resin.'
And, earlier this year, Charter NEX joined forces with Next Generation Films, Lexington, Ohio, to create a new platform focused on new specialty films products.
Charter NEX
877-411-3456
http://charternex.com
PACKAGING EQUIPMENT FOR ENTIRE LINE
BW Packaging Systems, Romeoville, Ill., exhibited a variety of equipment and technologies to showcase its ability to address requirements across the entire packaging line.
For instance, the Pneumatic Scale Angelus is a filler/seamer combination that leverages the strengths of the company’s flagship Hema and Angelus brands to include robust construction, hygienic design and production flexibility. This particular machine configuration includes electronic synchronization between the servo drives on the Hema filler and the Angelus seamer.
Accraply, Minneapolis, exhibited the Accraply 100 pressure-sensitive labeler along with a Graham and Sleevit DF60 tamper-evident shrink sleeve applicator. This configuration accurately labels even the most difficult applications. Toolless changeovers make these machines quick to configure—ideal to meet the demands of fast-moving production lines.
BW Packaging Systems
800-527-0494
www.bwintegratedsystems.com
ROBOTIC PICK-AND-LACE CELL, PALLETIZER
Quest Industrial, Monroe, Wis., highlighted its Quik Pick & Pack robotic pick-and-place cell and its Boxed-Bot robotic palletizer.
The Quest Quik Pick & Pack is a high-speed robotic case packer that’s quick, accurate and compact. Loaded with the QPack custom case packing software, the Quik Pick & Pack can be configured to pick up as many as 1,000 pieces per minute. The Quik Pick & Pack also works well with flexible film packaging, thanks to its vision system and optional 3D scanning that detects the pouches’ topography and center of gravity to identify the proper high point for picking. The Quik Pick & Pack also performs well with any packaging type that comes from a vertical form-fill-seal or horizontal flow wrapper machine. The Quik Pick & Pack handles a variety of product shapes, weights and sizes. The machine can pick and place bags weighing only 1 ounce and reach all the way up to 20 pounds. Additionally, end users can create their own pack patterns to accommodate customers’ different packaging requirements. Additional features include:
- Accepts a wide range of boxes or cases with continuous changeover from size to size.
- Accepts a wide range of product types, sizes and textures.
- Custom orientation of product, including pile stacks, base stacks, random cuts, shingle stack and 2-3 stack.
The Quest Boxed-Box skid-based robotic palletizer features a footprint starting at just 8x10 inches. The Boxed-Bot allows operators to design and produce exact pallet patterns quickly and easily from bags to boxes and other product types. Creating patterns is accomplished though the QBox custom pallet building software, what is said to be the most technologically-intuitive operator interface available on the market. The Boxed-Bot features a long-reach Fanuc M-710IC Series robot that provides higher stack patterns, which better maximizes tractor-trailer loading for more efficient shipping.
Furthermore, in April, ProMach, Cincinnati, acquired Quest Industrial to strengthen its robotics integration capabilities.
Quest Industrial
608-325-5850
https://questindustrial.com
TRAY PACKAGING & STRETCH WRAPPING MACHINES
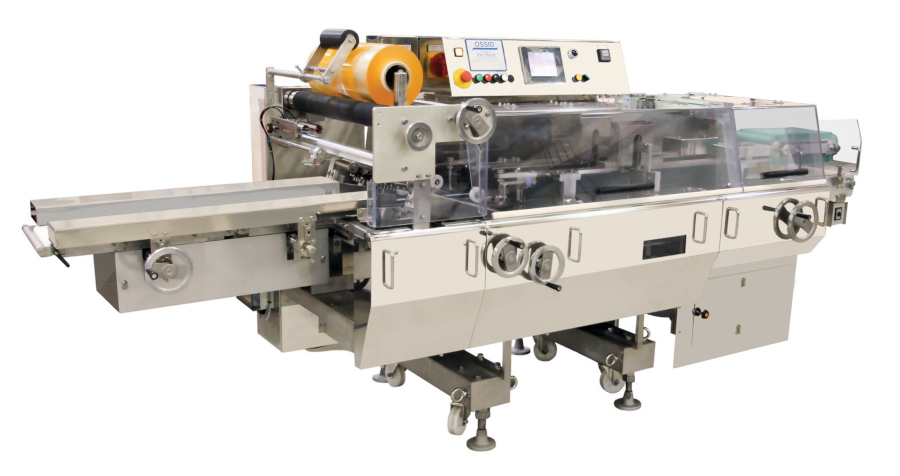
Ossid, Battleboro, N.C., showcased its lineup of tray packaging and stretch wrapping machines.
For instance, Ossid’s 500Si High-Speed Stretch Wrapper produces tightly wrapped, PVC case-ready packaging at speeds of up to 120 trays per minute for the poultry, meat and produce industries. The 500Si also uses less film and requires no air or water utilities during operation. Features include:
- Product changeover in less than two minutes.
- Runs tray sizes #2 to 8x15-inch standard.
- PVC stretch film capable.
- Stainless-steel construction.
- Gripper-chain system stretches shrink films to produce tightly wrapped packages.
- Servo-driven technology and microprocessors reduce downtime and maintenance.
The ReeTray 30 Semi-Automatic Tray Sealer can do three types of sealing—ambient tray sealing; modified atmosphere packaging (MAP); and vacuum skin packaging (VSP).
The ReeTray 30 Semi-Automatic Tray Sealer features a 2-chamber system for packaging products in standard #3 trays. The easy-to-use interface allows operators to select the type of sealing. Features include:
- Automatic film advance produces up to 24 packs per minute (depending on the size of the trays and number of trays per cycle).
- Rugged stainless-steel construction.
- Manual or semi-automatic drawer feed and interchangeable tooling for fast changeovers between tray sizes.
The ReeForm E40 Thermoformer features an all stainless-steel design for easy sanitation in washdown environments. The ReeForm E40 comes with a user-friendly control panel touch screen for easy setting and recording of different programs, and a control box for fast, efficient positioning and adjusting of bottom film. The ReeForm E40 also offers consistent pack quality at a higher level of speed to process flexible and rigid film with thickness up to 600 microns and film width up to 420 mm. It provides a maximum forming depth of up to 120 mm and a maximum cut-off length of up to 300 mm.
Ossid
800-334-8369
www.ossid.com